ISCC PLUS Certified Materials
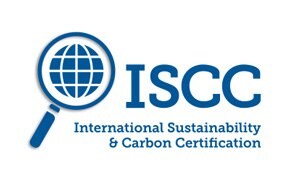
We're producing more sustainable plastics by incorporating polymers from renewable sources and decreasing our reliance on traditional petroleum sources. This shift gives us the opportunity to significantly reduce our carbon footprint for plastic production.
In 2024, we began the International Sustainability and Carbon Certification PLUS (ISCC PLUS) certification process at key manufacturing sites. As part of this process, we’ve implemented the mass balance approach to manage and track greener content in our supply chain. This approach allows us to integrate renewable feedstock into our plastics without affecting their performance. With third-party verification through ISCC PLUS certification, each production site will monitor the specific proportion of bio-renewable feedstock used in our plastics.
Key Benefits
- Same Material and Quality: The chemical composition of the plastic remains unchanged. The quality of the plastic has been shown to be indistinguishable from petroleum-derived plastics previously used for the same products.
- Lower Environmental Impact: By utilizing alternatives to fossil fuels, we decrease our reliance on non-renewable resources.
- Precise Monitoring and Transparency: Third-party verification accurately tracks the percentage of renewable materials, certifying the exact source of materials from the point of origin to final product for a fully traceable journey.
Leveraging cutting-edge technology in polymer production, we are improving the sustainability of our plastics-based product lines.
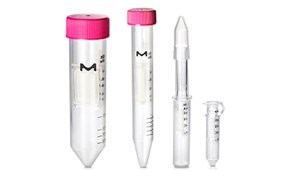
Amicon® centrifugal ultrafiltration devices were developed for concentration and diafiltration of biological and environmental samples in preparation for downstream applications. The filter devices are made from ISCC PLUS certified materials.
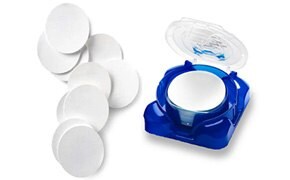
Millipore® membranes have supported laboratory filtration in academic, pharmaceutical, and industrial sectors since the 1950s. The membrane packaging is made from ISCC PLUS certified materials.
Frequently Asked Questions
What is the mass balance approach process?
Mass Balance is a way to track and manage recycled materials in chemical recycling. In this process, large plastic molecules are broken down into smaller pieces, which can then be used to create new products. A small portion of renewable feedstock (often <10%) is added during petroleum processing, including chemical production and monomer production. Products are labeled based on their overall allocation of renewable feedstock, not their individual composition.
There are two allocation methods to distribute the renewable feedstock across products. They are either: A) distributed across the entire production batch equally (proportional), or B) distributed to a proportion matching the renewable content added (non-proportional). Both methods use the same amount of renewable feedstock:
A) Proportional: Renewable feedstock is distributed in the same way as non-recycled materials. For example, if 10% renewable feedstock is added, then all products are 10% renewable.
B) Non-Proportional (Free Allocation): Renewable feedstock is distributed freely across any of the products produced. In this method, if 10% renewable feedstock is added to the overall production, up to 10% of the products can be labeled as 'bio-attributed', even though each individual product may contain less than 10% renewable feedstock. For example, it is possible that 10% of products can include 100% of the renewable feedstock, while the remaining products include 0%.
What are we using for renewable feedstock at our production sites?
The raw material is a bio-derived waste product, such as from used cooking oil or forestry residues.
To continue reading please sign in or create an account.
Don't Have An Account?