Drawable Carbon Nanotube Array for High-Performance Artificial Muscles and Energy Harvester
Na Li, Ph.D.
Global Product Manager for Electronic Materials
Drawable Carbon Nanotube Array
A drawable Carbon Nanotube (CNT) array is a special type of CNT forest, in which individual nanotubes are aligned and grown vertically on a substrate through a chemical vapor deposition (CVD) process. Most strikingly, a macroscopically aligned, pure, and pristine CNT sheet can be continuously drawn out of the array, parallel to the drawing direction, as a result of a delicate interactive force established between neighboring CNTs (Figure 1).
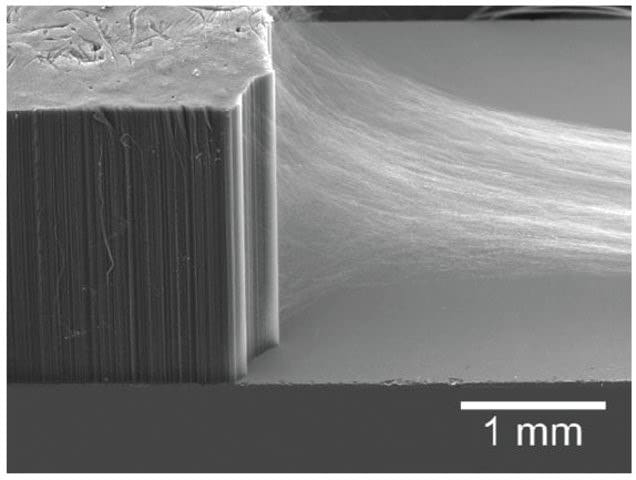
Figure 1.SEM of a drawable carbon nanotube array, with CNT sheet pulled out from the side.
Unlike other forms of CNTs, which require intensive and often destructive post-treatment before being assembled into usable forms, drawable CNT arrays offer an easy way to process CNTs into aligned sheets (films), twisted fibers, and conformal coatings, without degrading the properties of pristine CNTs. A typical individual CNT within the array has a very large aspect ratio (~50,000), and strong anisotropy. The multi-walled CNT has an outer diameter of ~20 nm (Figure 2) and a length of ~1 mm.
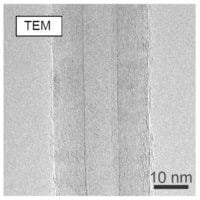
Figure 2.TEM of a typical carbon nanotube from the drawable CNT array
Twisted and Coiled Carbon Nanotube Yarn
Helical structures are commonly found in nature, from the spiral arms of the Milky Way to the double helix of DNA in our cells. The chiral, vortex-like structures are formed along a specific direction. Following this concept, inserting twist to an as-drawn CNT sheet consisting of millions of aligned carbon nanotubes, or to a stack of multiple such CNT sheets, helically winds and compacts CNTs into a densely twisted yarn (Figure 3). Carbon nanotubes themselves are highly anisotropic, their strength along the length is much greater than along the diameter, and the resulting twisted CNT yarn is helical and highly anisotropic. This leads to an important phenomenon: when volume expansion occurs in such a yarn system, it will no longer be isotropic, the volume expands to primarily increase the diameter of the yarn, rather than to extend its length (when the bias angle of the yarn is below a magic angle of ~55˚), and can often cause contraction along the length instead.
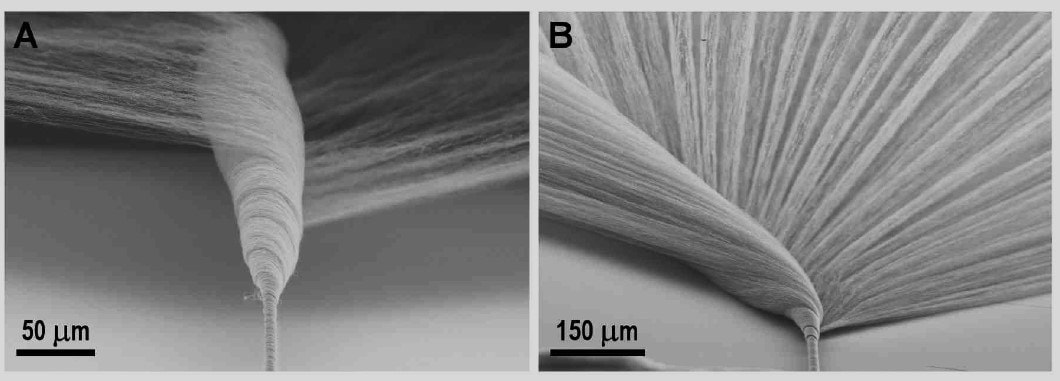
Figure 3.SEM of CNT yarn formation during twist insertion to an as-drawn CNT sheet from the array.
This helical twisted CNT yarn can be further converted into a tightly coiled structure, like that of an old telephone cord, or a metal spring (Figure 4), by further twist insertion or wrapping around a mandrel, and set in shape.
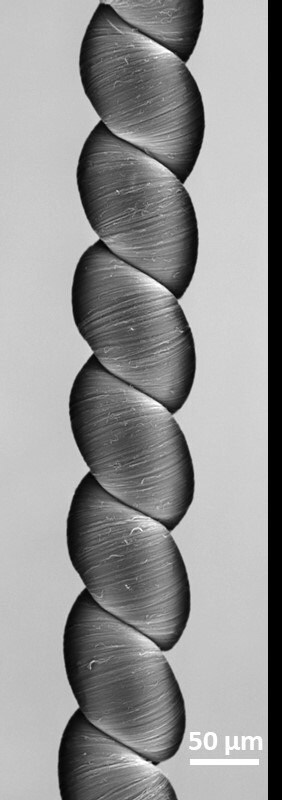
Figure 4.SEM of a coiled CNT yarn by further twisting a twisted CNT yarn
Artificial Muscle: Beyond Lifelike Power
Artificial muscles are smart actuator materials that change shape in response to external stimuli, and perform mechanical work, mimicking the behavior of natural muscles. Artificial muscle fibers could one day replace hard-to-miniaturize motors and bulky hydraulic actuators used in traditional robotics, making robots more human-like, and allowing safer interaction. In recent years, the twisted and coiled CNT yarns discussed above have emerged as promising artificial muscle fibers that do powerful work, even outperforming natural muscle in many ways.
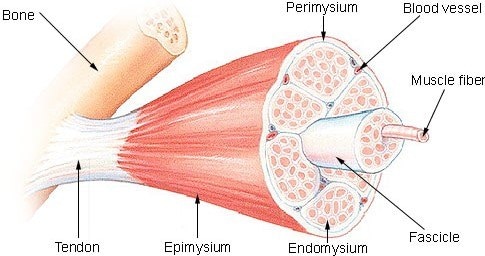
Figure 5.Structure illustration of natural skeletal muscle
There are two types of artificial muscles made from twisted and coiled CNT yarns: torsional artificial muscles, and tensile artificial muscles.
Torsional artificial muscles rotate when actuated in a CNT yarn, like an elephant trunk, with a much higher rotational stroke and speed. In a 2011 discovery, when a twisted 12-µm-diameter CNT yarn was half immersed in an electrolyte, and charged electrochemically, it provided 250%mm of rotation at speeds of up to 590 rpm.1 When infiltrated with a volume-expanding guest, such as paraffin wax, the wax-hybrid CNT yarn rotated at a speed of up to 11500 rpm,2 provided a gravimetric torque that is comparable to large electric motors, and cycled for ~2 million times without signs of degradation.2
Tensile CNT yarn artificial muscles behave most similarly to human skeletal muscle, only that they offer greater force and power than the same size and weight of natural muscle fiber. In a 2012 study, CNT yarns demonstrated tensile actuation after twisting to such an extreme degree that the yarns spontaneously formed coils (Figure 4). The coiled CNT yarns provided tensile contraction of ∼7.3% when electrothermally heated to incandescent temperatures in an inert environment. Furthermore, infiltrating CNT yarns with guest materials having a large coefficient of thermal expansion lowered the temperature required to cause actuation. A coiled CNT yarn infiltrated with paraffin wax delivered over 5% contractile stroke when heated to 200 °C.2
More recently, a coiled, silicone rubber-infiltrated CNT yarn was shown to provide a tensile stroke of more than 34% when heated electrothermally, and 50% when actuated by solvent absorption. During contraction, the coiled CNT yarn yielded specific work of 2.48 kJ/kg, which is more than 50 times that of natural skeletal muscle, and delivered an average power of 27.9 kW/kg over the full cycle, which is around 80 times that of natural skeletal muscle. The yarn performed for more than 1 million reversible cycles without any signs of degradation.
By choosing different stimuli-responsive, volume-changing materials as the guest, allows the engineering of smart hybrid CNT yarn torsional and tensile muscles that respond to different changes in cue, such as temperature, humidity, light wavelength, and the presence of a specific antigen through antigen-antibody recognition.2-6 Similar principles can be applied to fabricate twisted and coiled polymer fibers that are naturally anisotropic for the production of smart textiles that adjust porosity corresponding to environmental changes.7,8
Carbon Nanotube Yarn Energy Harvesters: Artificial Muscle in Reverse
Twisted and coiled carbon nanotube yarn artificial muscles work by converting different sources of energy into mechanical energy. For instance, an electrochemically actuated CNT yarn converts electricity into contraction and rotation. Can we generate electricity by deforming a twisted or coiled carbon nanotube yarn instead?
Indeed, stretching and releasing a coiled carbon nanotube yarn, or untwisting a twisted CNT yarn inside an electrolyte, reversible open circuit voltage changes can be measured. When short-circuited, reversible current changes can be obtained, converting mechanical energy into electricity.9 Figure 6 shows the successful illumination of an LED bulb in an external circuit by stretching a coiled CNT yarn immersed in a 0.1 M HCl electrolyte. Interestingly, unlike traditional dielectric elastomer mechanical energy harvesters that require kilovolts of bias voltage to work, this electrochemical process does not need any additionally applied bias voltage, since immersing the CNT yarn into electrolyte provides enough electrochemical potential differences for harvesting mechanical energy.
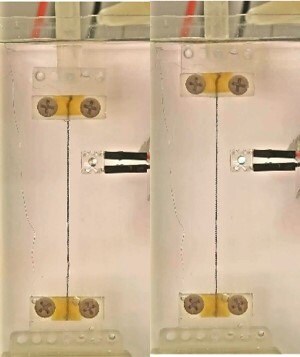
Figure 6.An LED light in the external circuit lit up by stretching a coiled CNT yarn inside an electrolyte, boosting the voltage
The observed mechanical energy harvested results from the reversible electrochemical capacitance change for the coiled CNT yarn during the stretch-release process. Due to the helical and anisotropic nature of the yarn, when stretched, the length increase of the coiled yarn is converted effectively into up-twist of the constituent twisted CNT yarn, causing tremendous torque and diameter decrease. It has been observed that this internal stress could deform CNT axially to minimize the surface energy of neighboring CNTs within the same bundle. Decreased electrochemically accessible surface areas correspond to a decrease of electrochemical capacitance. Experimentally, capacitance was measured to decrease reversibly to below 70%, thus generating electricity.
These twisted and coiled carbon nanotube yarn mechanical energy harvesters are ideal energy sources for self-powered wireless sensors in IoTs, eliminating the daunting task of repeatedly changing batteries for thousands of sensors. They are also able to power human health monitoring systems, and extract energy from ocean waves.
In summary, the drawable carbon nanotube array has opened the door to practical applications of carbon nanotubes and multifunctional CNT composites, enabling exciting future innovations.
Materials
References
To continue reading please sign in or create an account.
Don't Have An Account?