Polymer-Clay Nanocomposites: Design & Application
Dr. Alexander B. Morgan
Material Matters Volume 2 Issue 1
Why Use Polymer Nanocomposites?
One of the desirable end-goals of materials science research is the development of multi-functional materials. These materials are defined as compositions that bring more than one property enhancement to a particular application, thus allowing the material to replace more than one other material in an engineered object, or to replace entire classes of materials which alone, are only capable of addressing one end-use need. One example is aerospace wings and fuselages, which today are made of metal. A multi-functional material used to replace the metal would need to be lightweight, very durable to high stress/shear energies, fireproof, and able to conduct electricity to address lightning strike issues at high altitudes. Traditional polymer composites can meet the lightweight and durability requirements and are in use today on aircraft, but they must be combined with metallic meshes and interleaves to address lightning strikes, and they tend to have far worse flammability properties than the metal they replace. The use of nanoparticles in these polymer matrices, thus creating a nanocomposite, can yield an optimal multi-functional material for aerospace needs and other applications.
Polymer-Clay Nanocomposites
The polymer nanocomposite field has been studied heavily in the past decade, spawning numerous conferences, books, and journal articles. To some extent, it became a major field of study due to key papers from Gianellis and Vaia in the mid-90s1 and to the release of a commercial polyamide-6 clay nanocomposite by Ube/Toyota of Japan.2 It can be argued however, that polymer nanocomposite technology has been around for quite some time in the form of latex paints, carbon-black filled tires, and other polymer systems filled with nanoscale particles. However, the nanoscale interface nature of these materials was not truly understood and elucidated until recently. Today, there are excellent review papers and books that cover the entire field of polymer nanocomposite research, including applications, with a wide range of nanofillers such as layered silicates (clays), carbon nanotubes/nanofibers, colloidal oxides, double-layered hydroxides, quantum dots, nanocrystalline metals, and so on.3 The majority of the research conducted to date has been with organically-treated, layered silicates, or organoclays, and this short review article will focus on polymer nanocomposites made with these materials.
Before describing organoclay structure and chemistry, a rudimentary understanding of the polymer nanocomposite itself is required. A traditional composite containing micron or larger particles/fibers/reinforcement can best be thought of as containing two major components, the bulk polymer and the filler/reinforcement, and a third, very minor component, or interfacial polymer. Poor interfacial bonding between the bulk polymer and filler can result in an undesirable balance of properties, or at worst, material failure under mechanical, thermal, or electrical load. In a polymer nanocomposite, since the reinforcing particle is at the nanometer scale, it is actually a minor component in terms of total weight or volume percent in the final material. If the nanoparticle is fully dispersed in the polymer matrix, the bulk polymer also becomes a minor, and in some cases, a non-existent part of the final material. With the nanofiller homogenously dispersed in the polymer matrix, the entire polymer becomes an interfacial polymer, and the properties of the material begin to change. Changes in properties of the interfacial polymer become magnified in the final material, and great improvements in properties are seen. Therefore, a polymer nanocomposite is a composite where filler and bulk polymer are minor components, and the interfacial polymer is the component that dictates material properties. With this in mind, the design of the nanoparticle is critical to nanocomposite structure, and careful understanding of nanoparticle chemistry and structure are needed.
Organoclay Chemistry and Structure
Clays are a broad class of inorganic layered structures. They can occur naturally or be made via synthetic techniques. While many different clay structures have been used in the synthesis of organoclays and polymer-organoclay nanocomposites, the majority of the research has been accomplished with montmorillonite. Montmorillonite is a 2:1 aluminosilicate, meaning it is composed of an octahedral aluminum oxide layer sandwiched between two tetrahedral silicon oxide layers. In the octahedral layer, aluminum atoms are replaced with other cations (e.g., magnesium, iron), which creates some charge defects in the structure (Figure 1). This means that montmorillonite has cations associated with its structure to balance this charge in the octahedral layer, and these cations sit atop the silicate tetrahedral layer. Since there is no formal ionic bond between the anionic charge defect in the octahedral layer and the cation on top of the silicate layer (more of a charge association), the cations can be exchanged with other cations of similar charge to generate organically treated clays. Sodium cations on montmorillonite can ion exchange with alkyl ammonium, phosphonium, imidazolium, or any other +1 cation to yield an organoclay (Scheme 1). It should be noted that ion exchange with sodium montmorillonite is facile with many different cations, but cations with charges greater than +1 have a strong tendency to lock the clay plates together (a process called pillaring),4 which renders polymer nanocomposite synthesis impossible.
![Molecular model5 of Hydrated Montmorillonite clay [(Mg0.33Al1.67)Si4O10(OH)2]Na0.33]. The clay layers are separated by a layer of water molecules. Molecular model5 of Hydrated Montmorillonite clay [(Mg0.33Al1.67)Si4O10(OH)2]Na0.33]. The clay layers are separated by a layer of water molecules.](/deepweb/assets/sigmaaldrich/marketing/global/images/technical-documents/articles/materials-science-and-engineering/polymer-synthesis/polymer-clay-nanocomposites-figure1.gif)
Figure 1.Molecular model5 of Hydrated Montmorillonite clay [(Mg0.33Al1.67)Si4O10(OH)2]Na0.33]. The clay layers are separated by a layer of water molecules.
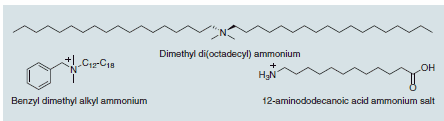
Scheme 1.Typical alkyl ammonium organic treatments
The organic treatment of the clay renders the normally hydrophilic montmorillonite hydrophobic, thus allowing it to interface with many different polymer matrices. Without this organic treatment, the montmorillonite would never disperse into the polymer and remain as micron-sized particles, serving as a traditional filler. The exception to this is when montmorillonite is dispersed in water and mixed with a water soluble polymer such as poly(vinyl alcohol). A good nanocomposite can then be obtained without organic treatment.6 For almost all other non-water soluble polymers, however, an organic treatment on the clay surface will be needed to obtain a polymer nanocomposite structure. The most commonly used organic treatment is an alkyl ammonium, which can have variety of chain lengths or functionality present, and can be a quaternized primary, secondary, or tertiary amine. The one common feature to a successful clay organic treatment is the presence of at least one long (12 carbons or more) alkyl chain, as without this microcomposites are typically obtained.7 Care must be taken when picking the organic treatment to allow polymer nanocomposite formation. Due to the variety of structures available, including those which enable polymerization or grafting involving the organic treatment, it is best to refer to the open literature before selecting an organic treatment with which to work. Guides do exist however,3,8 and these can aid the selection. One final note on organic treatment selection must be made, and that is to consider the thermal stability needed in the final material application. Alkyl ammoniums, while very successful in the synthesis and development of polymer nanocomposite materials, are thermally unstable above 200 °C, undergoing a Hofmann degradation at this temperature (Scheme 2).9 When this occurs, the polymer/clay interface is destroyed and the material can thermally rearrange to give a microcomposite structure, thus nullifying any gains achieved by the original nanocomposite structure.10 For higher temperature end use applications, imidazoliums (Scheme 2) appear to have great promise, capable of handling temperatures ; 300 °C and available in a variety of structures that can be tailored to the polymer nanocomposite application.11
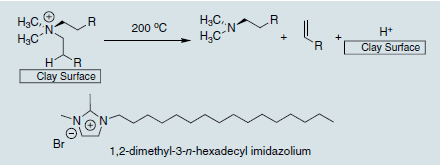
Scheme 2.Hofmann Degradation of alkyl ammonium on clay surface and thermally stable imidazolium cation treatment.
Selecting the Organoclay and Analyzing the Nanocomposite
Polymer clay nanocomposites show great promise for materials science applications, but the synthesis and successful development of these materials is not simple. Organoclays are not a “drop-in” solution; careful selection and consideration of the entire nanocomposite system must be undertaken before a successful polymer-clay nanocomposite (or any nanocomposite for that matter) can be prepared and utilized for a new materials science application. If the wrong organoclay is chosen for a particular polymer, the nanocomposite may never be formed, as the nanoparticles might not disperse well enough. Further, even if the best organoclay is chosen, poor mixing or synthetic processes can result in a failure to form a nanocomposite, and in some cases, may result in a material with properties worse than the starting polymer. Finally, the target application will dictate clay loading, or whether a clay is even acceptable for that final application. Therefore, designing the nanocomposite system on paper before actually going to the lab is recommended. Pick an organoclay that will be miscible with the polymer chosen,sup>12 and will survive the processing conditions. Finally, make sure that the clay property enhancements (mechanical, flammability, gas barrier, etc.) meet with the desired application for the final polymeric material.
Once the system is designed, the material can be prepared, but polymer nanocomposite analysis continues to be just as much a challenge as designing a successful nanocomposite in the first place. No one analytical technique gives all the necessary information about a polymer clay nanocomposite, and some techniques by themselves can give deceptive information on the nature of the clay nanocomposite structure and uniformity of dispersion. In particular, powder x-ray diffraction alone cannot provide the type of information that is required to characterize nanocomposite formation. Several key articles cover this area of nanocomposite analysis,13 and the researcher is strongly encouraged to read them before embarking on a nanocomposite synthesis program.
Once proper characterization has been obtained, then the researcher can determine if changes need to be made to the process of nanocomposite formulation, or if some other part of the system (such as the clay/polymer interface) is not welldesigned and new work is needed.
Polymer-Clay Nanocomposite Applications
Without going into detail on how the clay nanocomposites impart enhanced property performance, this article will focus on where clay nanocomposites have been used to improve property performance, especially to yield improvement in more than one area, and also where the improvements have led to commercial use. There will be some general discussion about how the properties are obtained, but details are best found in the cited articles or in the review papers cited earlier in this paper.3 The most common use of polymer-clay nanocomposites has been in mechanical reinforcement of thermoplastics, especially polyamide-6 and polypropylene. The aforementioned polyamide-6 clay nanocomposite produced by Ube/Toyota was used to replace a metal component near the engine block that yielded some weight savings. The clay in this application improved the heat distortion temperature of the material, allowing it to be used in this higher temperature application. GM/Blackhawk has also announced polypropylene-clay nanocomposites for automotive applications, and the clay brought an increase in flexural/tensile modulus while maintaining impact performance.
The use of polymer-clay nanocomposites for flame retardant applications is becoming more common, especially as it is realized that the clay nanocomposite can replace part of the flame retardant package while maintaining fire safety ratings at a lower flame retardant loading.14 This results in a better balance of properties for the nanocomposite material compared to the non-nanocomposite flame retardant product, and in some cases, better cost for the flame retardant resin, especially if the organoclay is cheaper than the flame retardant it is replacing. It should be noted that the organoclay can replace traditional flame retardant on more than a 1:1 by weight basis, meaning 1 g of organoclay can replace more than 1 g of traditional flame retardant, resulting in a lighter material. In fact, it appears that clay nanocomposite systems serve as a nearly universal synergist for flame retardant additives, with some exceptions.14 The synergistic enhancements of clay nanocomposites for fire safety applications has led to two commercial products: a Wire & Cable jacket material (organoclay + aluminum hydroxide) produced by Kabelwerk Eupen AG, and a series of polypropylene + organoclay + flame retardant systems (Maxxam™ FR) produced by PolyOne®. It is likely that other commercial materials will be released soon as more manufacturers begin to see the value of these nanocomposite systems.
Another common application of clay nanocomposites is for gas-barrier materials. Clay nanoparticles create a complex network in the polymer matrix, such that various gases either diffuse very slowly or not at all through polymer chains and pinholes in thin films or thicker polymer parts. The success of clay nanocomposites to impart decreased diffusivity of oxygen and water has led to their use in food/liquid packaging to keep foods fresher longer.3
Future Applications
Polymer clay nanocomposites are already used in many applications to enhance existing properties of a particular material, and further R&D efforts should focus on development of true multi-functional materials. Certainly, clay nanocomposites will continue to be used for enhanced mechanical, flammability, and gas barrier properties, but fundamental limits in clay chemistry prevent them from being used easily in applications requiring electrical/thermal conductivity or optical applications. Along those lines, combinations of organoclays with other nanofillers to obtain a true multi-functional material will likely arise in the future. Combining an organoclay with carbon nanotubes, or quantum dots, could yield a very interesting nanocomposite with enhanced mechanical, flammability, thermal, and electrical properties – allowing it to be a drop-in replacement for many different materials in a complex part. Or, the clay could enhance the properties of some existing mechanically fragile system while keeping other properties intact. Some early initial research has been done on combining more than one type of nanofiller in a polymer matrix, but this approach has not yet been widely studied.
The field of polymer-clay nanocomposites, and the broader field of polymer nanocomposites, continues to grow. As stated in the introduction, these materials have likely been in use for quite some time already, but as the chemist and materials scientist become better at designing the system through fundamentals, new products and applications utilizing this technology will grow in number and capability.
References
To continue reading please sign in or create an account.
Don't Have An Account?