Mesoporous Materials Synthesis
Mespoporous materials, also known as mesoporous molecular sieves, are a class of 3D-nanostructures with well-defined mesoscale (2–50 nm diameter) pores and surface areas up to 1000 m2/g.1 In terms of characteristic ordered feature size, they occupy a unique place between crystalline zeolites and other types of 3Dstructured materials described in this issue, e.g. 3DOM and direct-write materials with features > 100 nm. Mesoporous materials are formed by a self-assembly process from combined solutions of sol-gel precursors (e.g. metal alkoxides) and structure-directing amphiphiles, usually block-copolymers or surfactants (Figure 1).2,3Flexible, “one-pot synthesis” employing self-assembling templates enables the simultaneous control of size and 3D geometry (mesophase) of the pores. Furthermore, surface functionality of the pores can be modified by adding organically modified precursors, for example organosiloxanes RSi(OR’)3 or bis(organosiloxanes) (R’O)3Si- R-Si(OR’)3, to the initial reaction mix.4 On the other hand, it is relatively difficult to control long-range order and orientation of self-assembled structures and they typically have more defects and less structural precision compared to 3DOM or direct-write materials.
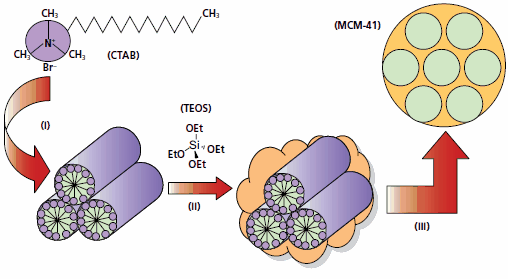
Figure 1.Schematic of the classical mesoporous silica (MCM-41) synthesis route.2 (i) Surfactant, e.g. cetyltrimethylammonium bromide (CTAB, Product No. 52370), is used to form liquid crystalline micelles in water. (ii) Ceramic sol-gel precursor, e.g. tetraethylorthosilicate (TEOS, Product No. 131903), is added to this micellar solution to make, upon hydrolyses and condensation, a silica network around the micelles. (iii) Removal of the organic template by thermal treatment (calcination) or solvent extraction yields a mesoporous ceramic material, in this case hexagonally ordered MCM-41 silica framework.
Relative advantages of a given 3D-structure preparation route govern the resulting material applications. Ordered mesoporous materials templated by “soft” amphiphilic templates overcome pore size constraints of zeolites to allow more facile diffusion of bulky molecules. This lends them to applications in catalysis and absorption technologies where requirements for long-range material order can be less important. For example, acidic aluminosilicates are investigated for uses in fluid catalytic cracking and condensed-media chemical conversion processes.5 Surfacefunctionalized mesoporous sieves can be used in active elements of sensors.6 Large, optically active molecules, such as dyes7 (e.g. rhodamine 6G, Product No. 252433) and conjugated polymers8 (MEH-PPV, Product No. 541443) can be incorporated into mesoscale pores to make hybrid materials with unique optoelectronic properties.
In addition to ready-made materials, we offer reagents for your own unique synthesis of mesoporous structures. Cationic quaternary ammonium surfactants are often used to prepare mesoporous silicates under basic hydrothermal conditions. Anionic surfactants are employed for aqueous synthesis of mesoporous alumina and for basic syntheses with added positively charged counterions or co-structure directing agents.9,10 Nonioninc surfactants can be used to prepare disordered wormhole silicas (HMS, MSU) or ordered silicas under acidic conditions.3 Highly ordered mesoporous materials with uniform pore sizes larger than 5 nm can be made with PEG-PPG-PEG (Pluronic) triblock copolymers as templates in acidic aqueous media.11
Materials
References
To continue reading please sign in or create an account.
Don't Have An Account?