Electrode Materials for Lithium Ion Batteries
Kinson C. Kam, Marca M. Doeff
Lawrence Berkeley National Laboratory, Environmental Energy Technologies Division, University of California, Berkeley, California 94720
Background
In 2010, the rechargeable lithium ion battery market reached ~$11 billion and continues to grow.1 Current demand for lithium batteries is dominated by the portable electronics and power tool industries, but emerging automotive applications such as electric vehicles (EVs) and plug-in hybrid electric vehicles (PHEVs) are now claiming a share. It is now possible for consumers to buy lithium ion battery-powered EVs such as the Tesla Model S sedan or Coda, or PHEVs like the Chevrolet Volt or Fisker Karma. For further market penetration, however, experts agree that prices of the batteries will need to come down, and performance and reliability will need to be improved.
The development of Li ion devices began with work on lithium metal batteries and the discovery of intercalation positive electrodes such as TiS2 (Product No. 333492) in the 1970s.2,3 This was followed soon after by Goodenough's discovery of the layered oxide, LiCoO2,4 and discovery of an electrolyte that allowed reversible cycling of a graphite anode.5 In 1991, Sony commercialized its first rechargeable lithium ion batteries combining a LiCoO2 (Product No. 442704) cathode with a
graphite (Product No. 496588) anode.6 In this dual intercalation system, also known as a "rocking chair" device, reversible insertion and removal of lithium ions into the electrodes are used as a means to store and deliver charge (Figure 1).
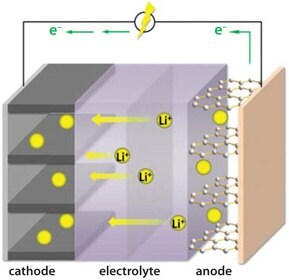
Figure 1.Schematic showing a Li ion battery containing an intercalation cathode on an Al current collector, an electrolytic solution containing a lithium salt, and a graphite anode on a Cu current collector.
Electric current is generated when lithium ions migrate from the negative electrode (anode) to the positive electrode (cathode) through the electrolyte during discharge. Reversing this process results in intercalation of lithium ions back into the anode and their removal from the cathode to produce the charged state. (In practice, cells are first assembled in the discharged state and charged prior to use). Careful cell engineering and improved packaging has resulted in a doubling of energy density over the past 20 years. However, the desire for lower cost and improved performance both for consumer electronic devices and those intended for automotive applications have led researchers to search for and develop alternative cathodes and anodes in the intervening years. Automotive applications, in particular, have stringent requirements for safety, cost, lifetime, and other performance metrics. Goals vary somewhat with the particular application (EV, PHEV, etc.) and a quantitative list can be viewed at: http://www.uscar.org/guest/article_view.php?articles_id=85 for the interested reader. Although increased energy density is an extremely desirable criterion, safety, calendar and cycle life considerations have sometimes trumped this requirement. Several new electrode materials have been invented over the past 20 years, but there is, as yet, no ideal system that allows battery manufacturers to achieve all of the requirements for vehicular applications. The state of the technology at present is such that there are several competing configurations utilizing different electrode materials, intended for different applications.
Commercial Battery Electrode Materials
Table 1 lists the characteristics of common commercial positive and negative electrode materials and Figure 2 shows the voltage profiles of selected electrodes in half-cells with lithium anodes. Modern cathodes are either oxides or phosphates containing first row transition metals. There are fewer choices for anodes, which are based on either graphite or the intercalation compound Li4Ti5O12 (Product No. 702277). These materials are lightweight, resulting in high specific capacities and energy densities, and generally perform well, although all have some drawbacks.
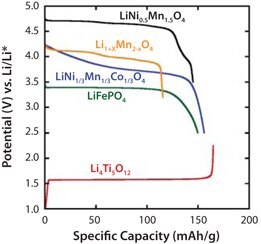
Figure 2.Voltage profiles of selected electrode materials in lithium half-cells.
A. Average
Cathodes
The first intercalation oxide cathode to be discovered, LiCoO2, is still in use today in batteries for consumer devices. This compound has the α-NaFeO2 layer structure (space group R3-m), consisting of a cubic closepacked oxygen array with transition metal and lithium ions occupying octahedral sites in alternating layers (Figure 3). The potential profile of LiCoO2 in lithium half cells is gradually sloping, and about half the lithium can be removed below 4.2 V vs. Li/Li+, to give a specific capacity of 140 mAh/g. Higher capacities can be achieved by increasing the charge voltage limit but this has detrimental effects upon cycle life7 due to structural instability of the highly delithiated LixCoO2 compound and irreversible electrolyte oxidation. Resource limitations, the high cost of Co, and the need for higher energy density spurred researchers to investigate other layered transition metal oxides. Out of this research, two new electrodes emerged: LiNi0.8Co0.15Al0.05O2 (or NCA)8,9,10,11 (Product No. 760994) and LiNi1/3Mn1/3Co1/3O2 (or NMC)12 (Product No. 761001). They are isostructural to LiCoO2 but have higher specific capacities. The structural, chemical, and thermal stabilities are also improved compared to LiCoO2.13 The small amounts of Co in these compounds reduce cost and improve the structure of the materials, compared to the parent compounds (LiNiO2 for NCA and LiNi0.5Mn0.5O2 for NMC). The incorporation of Al in NCA improves the thermal stability, although there are still safety concerns. Low-level partial substitution of Al for Co in NMC also has been shown to improve thermal behavior14 and cycling stability,15 while the addition of small amounts of Ti appears to increase practical capacities and improves cycling over an extended voltage range.16,17
In the Li-Mn-O system, spinels related to the stoichiometric compound LiMn2O4,18,19 (Product No. 482277) are the most technologically important, because LiMnO2 with the R3-m structure cannot be synthesized directly. While ion exchange of layered NaMnO2 can be used to produce LiMnO2 indirectly, it converts to spinel rapidly when cycled in lithium cells.20 LiMn2O4 has a cubic structure (space group Fd-3m) with Mn located in octahedral 16d sites and Li ions on 8a tetrahedral sites in a cubic close-packed array of oxygen anions (Figure 3). Insertion of Li ions into vacant octahedral sites occurs below 3 V vs. Li/Li+ and produces the Jahn-Teller distorted tetragonal phase, Li2Mn2O4. There is a 16% elongation of the c-axis upon phase conversion, which causes fracturing and disconnection of particles, and results in rapid capacity fading upon cycling. Removal of Li from the 8a sites to form the delithiated phase, λ-MnO2, is much more reversible and occurs above 4 V vs. Li/Li+. Thus, cycling is restricted to the 4 V region, resulting in a theoretical specific capacity of 148 mAh/g for the stoichiometric compound. In practice, lithium-rich (Li1+xMn2-xO4) or Al-substituted modifications,21,22 which have better performance characteristics than LiMn2O4, are used commercially. The partial substitution of Li or Al for Mn results in lower theoretical capacities, but greatly decreases the risk of inadvertent overreduction of Mn below an average oxidation state of 3.5 during cycling, which is associated with production of the Jahn-Teller distorted tetragonal phase. While the performance of manganese oxide spinel electrodes has been greatly improved since they were first reported, they do not cycle as well as other oxides and LiFePO4, especially when subjected to elevated temperatures, because of the tendency for Mn to dissolve into the somewhat acidic electrolyte. Capacity fading is modest when spinel electrodes are cycled in lithium half-cells, but more evident in full cells with graphite anodes. This is attributable to the precipitation of dissolved manganese on the graphite anode and disruption of the solid electrolyte interface (SEI). Strategies to ameliorate dissolution include coating particle surfaces23 and the use of non-fluorinated electrolyte salts,24,25 and have met with some success. In spite of the cycling performance issues, the low cost and great abundance of Mn and the high power capability of spinel electrodes make them attractive choices for vehicular and some consumer device applications.

Figure 3.Structures of common electrode materials. From left to right, top: layered LiMO2 (M=Co, Ni, Mn), spinel structures of LiMn2O4 and Li4Ti5O12, and olivine LiFePO4. From left to right, bottom: graphite, Li2FeSiO4, and the layered-layered composite xLi2MnO3•(1-x) LiNiyMnyCo1-2yO2. Yellow spheres represent Li ions in these structures and MOx units are shown as colored polyhedra. C atoms in graphite are represented as white spheres.
In 1997, the phospho-olivine LiFePO4 was first reported as a cathode material.26 Its orthorhombic structure contains FeO6 octahedra and PO4 tetrahedra networked together to form 1D channels allowing lithium to diffuse along the b-axis (Figure 3). The theoretical specific capacity is ~170 mAh/g and the discharge profile is flat at ~3.45 V (Figure 2), characteristic of a two-phase reaction (LiFePO4 ↔ FePO4 + e- +Li+). The poor utilization and rate capability27,28 initially reported for this material in electrochemical cells was attributed to its low electronic conductivity and poor transport properties. Nanostructuring and carbon-coating of particles have greatly improved performance, and LiFePO4 is now considered one of the highest performance electrode materials available.29 Because the addition of electrochemically inert carbon reduces practical energy density, care must be taken to minimize the amount of coating on particles.30,31 Likewise, nanoparticulate powders frequently do not pack well, requiring additional binder and conductive additives in the electrodes, which reduces practical energy density further. Hierarchical structuring, in which small primary particles are organized into larger secondary ones, improves the energy density penalty somewhat. Figure 4 shows an example of a hierarchically structured composite of LiFePO4/C with excellent electrochemical performance.32
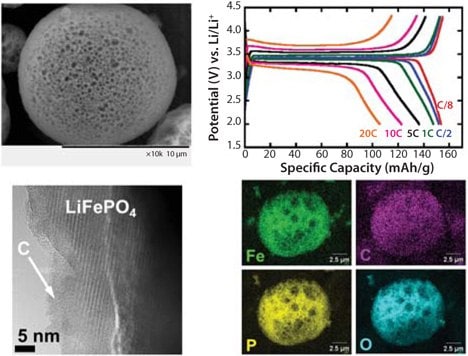
Figure 4.Upper left: scanning electron micrograph showing porous LiFePO4/C particle. Lower left: transmission electron micrograph of an internal surface of a LiFePO4/C particle showing a thin amorphous carbon coating. Upper right: rate capability of Li cells containing the LiFePO4/C composites. Lower right: elemental mapping of LiFePO4/C particle, showing homogeneous distribution. Modified figure from reference 31 used with permission.
Despite its relatively low energy density, the safety characteristics of the LiFePO4 electrode make it attractive for some vehicular applications. The charged material, FePO4, does not evolve oxygen upon heating, but rather converts to an electrochemically inert quartz structure with the same composition.33 The low voltage at which it operates also means that reactivity with the electrolyte and the associated safety issues are not as much of a concern as they are with the higher voltage oxide electrodes discussed previously. The low reactivity is what has allowed the success of a nanostructuring approach for LiFePO4 electrodes. In contrast, nanostructuring of the higher voltage oxide electrodes often leads to accelerated capacity fading upon cycling as well as safety concerns due to increased reactivity of electrolyte with the high surface area particles and accelerated oxygen release. Figure 5 shows an example of this phenomenon; a nanostructured NMC exhibits higher capacity fade than a conventionally prepared material when cycled to 4.7 V in lithium half-cells.
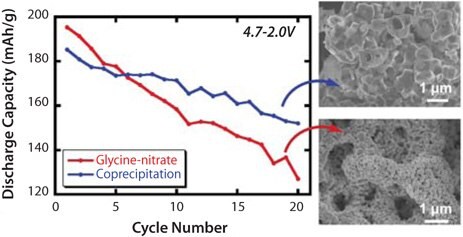
Figure 5.Capacity as a function of cycle number for cells cycled at 0.1 mA/cm2 between 4.7−2.0 V, containing two different LiNi1/3Mn1/3Co1/3O2 samples, one made by glycinenitrate combustion, which produces nanoparticles, and the other by a coprecipitation method, which results in micron-sized particles.
Anodes
At present, there are only two types of commercialized anode materials: those based on carbon (primarily graphite) and the oxide spinel Li4Ti5O12 (Figure 3). The use of a low potential intercalation electrode avoids the cycling and safety issues associated with dendrite formation on lithium anodes undergoing recharge, which have stymied their use in rechargeable batteries. Under normal operating and most abuse conditions, lithium dendrites do not grow on graphite anodes, and these electrodes can be cycled reliably. The chemical preparation of the graphite intercalation compounds (GICs) LixC6 (x=1), in which lithium ions are located between graphene sheets, was first reported in 1955 by Hérold.34 While lithiated graphite was proposed for use in batteries as early as 1977 by Armand and Touzain,35 solvent co-intercalation and irreversible reduction of the electrolytic solutions commonly used at the time prevented electrochemical cycling of this electrode. It was not until electrolytic solutions containing ethylene carbonate (EC) (Product No. 676802) were developed that graphite anodes could be used successfully in a lithium ion battery configuration. In these solutions, a solid electrolyte interface (SEI) forms on particle surfaces as graphite is lithiated in electrochemical cells during early cycles. The SEI is ionically conductive but electronically insulating, and, once formed, effectively prevents further irreversible reduction of the electrolytic solution. Some of the electrolyte is necessarily consumed during initial cell cycling to form the SEI, resulting in charge inefficiency. Careful purification, optimization of particle morphologies, and the use of electrolyte additives have reduced the inefficiency considerably; as a result, advanced Li ion batteries exhibit initial irreversible capacities of only a few percent. Precipitation of dissolved metal originating from the cathode or high temperature excursions during operation may disrupt the SEI, thereby necessitating its re-formation; this then results in further loss of cycleable lithium.
Graphite consists of graphene sheets staggered in either an AB (hexagonal, the most common form) or ABC (rhombohedral) stacking arrangement (Figure 3). Upon insertion of lithium ions, the graphene sheets stack directly on top of one another in an AA arrangement, and staging occurs; i.e. compounds form in which there are periodic arrays of unoccupied galleries, with the number dependent on the value of x in LixC6. (For example, in the stage 2 compound where x=0.5, occupied galleries alternate with unoccupied ones). Staging is manifested in the electrochemical voltage profile of lithium/graphite half-cells as a series of plateaus from about 0.2−0.1 V, indicative of several two-phase regions.
Non-graphitic carbons, which contain graphene domains but do not have long-range structural order, are also of interest for lithium ion batteries. Lithium insertion into these materials usually occurs at higher potentials than graphite, and staging does not occur. While the irreversible capacities are often much higher than with graphite, the SEI on some types of disordered carbon (e.g., hard carbons) are less susceptible to disruption, making them suitable for pairing with manganese oxide spinel cathodes in which metal dissolution can be problematic. The structures of disordered carbons are highly complex, and the electrochemical properties (shape of the voltage profile and capacity) vary considerably. For further information on carbon anodes, the reader is directed to references 36 and 37.
The spinel lithium titanium oxide, Li4Ti5O12,38 (Prod. No. 702277) is an alternative to carbon anodes, but its use is restricted to applications that do not require high energy density because of its high operating voltage (1.5 V vs. Li/Li+). It reversibly accommodates lithium to form the rock salt phase, Li7Ti4O12. Unlike most other intercalation electrodes, this material exhibits no volume change during the two-phase lithium insertion/extraction processes, making it a zero-strain material that cycles extremely well.39 Additionally, a high operating potential occurs within the thermodynamic stability window of organic carbonate-based electrolytic solutions, so that it is not necessary to form an SEI layer for proper functioning of the electrode. Because Li4Ti5O12 has intrinsically low electronic conductivity, it is often nanostructured. As with LiFePO4, the low reactivity of Li4Ti5O12 is what allows this approach to succeed, although concerns about the effect of nanostructuring on the already low energy density are still warranted. Best results are obtained when nanoparticles are uniform and spherical so that they pack well.40 Cells consisting of nanostructured Li4Ti5O12 and LiFePO4 could be cycled over 200 times at rates up to 10 C (where C is defined as the rate at which the total capacity of the cell is discharged in 1 hour) with no capacity fading.
Toward Better Batteries
Current research on electrodes for Li ion batteries is directed primarily toward materials that can enable higher energy density of devices. For positive electrodes, both high voltage materials such as LiNi0.5Mn1.5O4 (Product No. 725110) (Figure 2) and those with increased capacity are under development. The latter include the high capacity manganese-rich (HCMR) layered-layered composites with the general formula xLi2MnO3•(1-x)LiNiyMnyCo1-2yO2,41 and compounds such as Li2MSiO4 (M=Fe, Mn, Co) in which more than one Li per formula unit can, in theory, be removed. For the layered-layered composites, an initial charge above about 4.4 V vs. Li/Li+ in electrochemical cells activates the normally inert Li2MnO3 component by removing lithium ions and oxygen irreversibly. The layered "MnO2" moiety that is formed can then intercalate lithium ions, adding its capacity to that of the NMC component. While very high capacities (sometimes in excess of 250 mAh/g) have been reported for the activated composites in electrochemical cells, they suffer from poor rate capability and voltage decay due to the gradual conversion of the layered MnO2 component to spinel upon cycling.
The high theoretical capacity of about 330 mAh/g calculated for Li2MSiO4 based on extraction of two lithium ions per formula unit requires an overall redox state change of +2 for the initially divalent metal center. First principles calculations indicate that oxidation of Fe3+ to Fe4+ occurs at an impractically high potential,42 and experiments have verified that only the first lithium ion can be extracted during charge of Li2FeSiO4 in electrochemical cells.43 While the oxidation of Mn3+ to Mn4+ in the silicates is expected to occur at lower potentials than that of Fe3+ to Fe4+, attempts to use Li2MnSiO4 or Li2(Mn,Fe)SiO4 compounds as cathodes have not met with much success. Even nanostructuring and the addition of large amounts of carbon to composite electrodes do not sufficiently compensate for the poor transport properties and have a negative impact on practical energy density. In addition, the wide voltage range over which the intercalation processes occur is undesirable since it leads to a decay of power capability as the electrode discharges. Compounds in which metal centers can undergo more than one change in oxidation state remain of interest because of the potential for very high capacities, and researchers are continuing to search for electroactive materials with these characteristics.
In contrast, the high voltage spinel cathode LiNi0.5Mn1.5O4 exhibits very good rate and cycling performance without requiring nanostructuring,44 although the energy density advantage over commercially used materials is relatively modest (only about 30% greater than for Li1+xMn2-xO4, for example). The high operating potential may require the use of specially designed electrolytic solutions, coatings on particle surfaces, and other strategies to reduce coulombic inefficiencies and prolong cycle life. As with the isostructural LiMn2O4 variants, dissolution of Mn is potentially a problem for cycle life. This phenomenon, in both cases, is associated with the presence of electroactive Mn3+. In the idealized structure of LiNi0.5Mn1.5O4, Mn ions are in the +4 oxidation state and are electrochemically inert, and only Ni undergoes redox processes. In practice, samples usually exhibit some degree of nonstoichiometry, with excess Mn present in the trivalent state. This is manifested in the potential profile as capacity at about 4 V vs. Li/Li+ (Figure 2).
Research into new anode materials has been focused on Li alloys, primarily with Si,45 (Product No. 633097) and a class of materials known as conversion electrodes,46 which undergo Reaction 1 rather than simple intercalation.
nLi+ + ne– + Mn+Xm ↔ M + nLiXm/n (X=O, F, N, S) (1)
The starting materials for Reaction 1 are generally nanoparticulate, allowing facile reduction to the metallic element and lithium salt during lithium incorporation. Specific capacities can be extremely high (700 mAh/g or more), but these electrodes are plagued by high first-cycle inefficiencies, sloping voltage profiles, and large charge/discharge polarizations (hysteresis) leading to poor round-trip efficiencies. The hysteresis is most likely intrinsic to the system rather than a simple matter of kinetic limitations, which presumably could be ameliorated by nanostructuring. Bond breaking and re-formation occurs during the electrochemical processes, and reaction pathways may not be the same for charge and discharge.
The silicon/lithium system has the highest specific capacity of any lithium alloy, 4,200 mAh/g, corresponding to reduction all the way to the end-member composition of Li4.4Si. The very large volume changes associated with alloying (up to 400%) lead to rapid degradation and disconnection in composite electrodes prepared from conventional micron-sized silicon so that cycle life is poor.47 The volume changes also result in large coulombic inefficiencies associated with the continual formation of SEI layers on freshly exposed surfaces. Considerable efforts have been made to lower the volume expansion by nanostructuring Si to reduce mechanical stresses during the lithium alloying/de-alloying processes.48 Other strategies that have met with some success include the use of special binders that provide elasticity to the composite electrode,49 as well as conductive polymers which serve a dual purpose as binder and conductive additive.50
Small amounts of silicon are currently added to commercial anodes to boost capacity, and several battery companies have announced their intentions to replace graphite with silicon. Somewhat surprisingly, the improvement in specific energy of batteries containing Si anodes is expected to be only about 30%, in spite of the fact that the specific capacity of silicon is more than ten times greater than that of graphite. This is because of the requirement for capacity matching of the anode and the much less energy dense cathode, which must provide all of the cycleable lithium in the battery. Further increases in specific energy are, therefore, contingent upon successful development of a higher capacity cathode.
Summary and Challenges
The need for improved lithium ion batteries for demanding vehicular applications provides both challenges and opportunities for the interested materials scientist. While higher energy density is extremely desirable for these applications as well as for consumer electronics, it cannot come at the cost of safety, cycle life, or calendar life (Figure 5). For this reason, nanostructuring works best when used on materials with low reactivity, such as LiFePO4 and Li4Ti5O12, which have now been commercialized. A nano approach also appears to have some merit for silicon anodes, which are in an advanced stage of development. In addition to silicon, new high-energy density electrodes such as layered-layered oxide composites, high voltage spinels, conversion materials, and multivalent redox compounds including but not limited to silicates have recently emerged on the battery landscape.
Acknowledgment
This work was supported by the Assistant Secretary for Energy Efficiency and Renewable Energy, Office of Vehicle Technologies of the U.S. Department of Energy under Contract No. DE-AC02-05CH11231. This document was prepared as an account of work sponsored by the United States Government. While this document is believed to contain correct information, neither the United States Government nor any agency thereof, nor the Regents of the University of California, nor any of their employees, makes any warranty, express or implied, or assumes any legal responsibility for the accuracy, completeness, or usefulness of any information, apparatus, product, or process disclosed, or represents that its use would not infringe privately owned rights. Reference herein to any specific commercial product, process, or service by its trade name, trademark, manufacturer, or otherwise, does not necessarily constitute or imply its endorsement, recommendation, or favoring by the United States Government or any agency thereof, or the Regents of the University of California. The views and opinions of authors expressed herein do not necessarily state or reflect those of the United States Government or any agency thereof or the Regents of the University of California.
References
To continue reading please sign in or create an account.
Don't Have An Account?