Graphene-Based Composites and their Unique Renewable Energy Applications
Section Overview
Introduction
Graphene is a unique two-dimensional (2D) structure of monolayer carbon atoms packed into a dense honeycomb crystal that has attracted great interest due to its diverse and fascinating properties.1 Since it was first isolated in monolayer form in 2004,2 more and more mechanical, physical, and chemical routes have been developed to produce graphene. Of these diverse methods, chemical production of graphene is currently the lowest-cost method and is becoming a preferred mass production method. Currently, three major carbon sources are used as starting materials for the chemical production of graphene: 1) chemical reduction of graphite oxide (GO);3,4 2) sieved graphite powder (SGP);5–8 and 3) expanded graphite (EG).9–12 Although chemically reduced GO (rGO) (777684) contains a significant number of oxygen-rich functional groups favorable for surface decoration, the large number of defects that exist in the graphene lattice is irreversible.13–16 Comparatively, graphene sheets exfoliated from EG and SGP exhibit high electrical conductivity due to relatively low crystallographic defect densities.17
In view of its high surface area-to-mass ratio (2,600 m2/g),18 superior charge-carrier mobility (2×105 cm2/V s),19 excellent tensile strength of 130 GPa,20 and thermal conductivity of (4.84~5.30)×103 W/m・K,21 graphene is considered an ideal substrate for growing and anchoring various metal and metal oxide nanocrystals (NCs) to form high-performance nanocomposites. The manufacturing of such graphene hybrids requires that graphene sheets not only be produced inexpensively and in large quantities, but also that the attached metal/metal oxide NCs be incorporated and homogeneously distributed on the graphene surface. This article highlights the production, structure, and performance of three different types of grapheme-based composites, including: 1) graphene decorated with transition metal (Fe, Mn, Co) oxide NCs; 2) graphene decorated with noble metal (Pt) and Pt-based alloy; and 3) graphene decorated with TiO2 NCs. Their specific renewable energy applications—energy storage, energy conversion, and energy production—will also be examined.
Hybridization of Graphene with Transition Metal (Fe, Mn, Co) Oxides for Energy Storage Devices
Supercapacitors are very promising electrochemical devices for storing and releasing energy. Supercapacitors offer high power density, rapid charge and discharge, superior cycle lifetime, high reliability, and extremely low internal discharge. Over the past few decades, transition metal oxide NCs, such as MnOx,22–24 RuO2,25,26 and Fe3O4,27,28 have been thoroughly investigated as electrode materials for use in redox-based pseudocapacitors because of their high theoretical capacitance, abundance, and environmentally friendly nature. However, their high electrical resistance and poor electrochemical reversibility have limited their energy storage capacity for practical applications. Recently, carbon materials such as activated carbon, carbon nanotubes, and graphene have been demonstrated as promising materials for electrochemical double-layer capacitors (EDLC).29–32 Due to its high specific surface area and high electrical conductivity, graphene can act not only as a substrate for better distribution of transition metal oxide NCs, but also as a direct conductive path for rapid electron transmission. The hybrid of conductive graphene with transition metal oxide NCs has generated interest because of the potential for a synergistic effect on device performance. The welldispersed transition metal oxide NCs on the graphene can effectively prevent the stacking of graphene sheets, leading to higher available surface areas for the charge storage. The use of high-quality exfoliated graphene as a conductive substrate not only provides efficient electron transfer channels for attached NCs, but also contributes double-layer capacitance to the overall energy storage and, therefore, has great potential for improving the energy storage capacity of supercapacitors. During the past decades, various methods have been developed to hybridize transition metal oxide NCs on GO.33–40 Yan et al. developed a solvothermal approach for decorating the reduced GO with Fe3O4 NCs and proved that the capacitance of composites is much higher than that of pure reduced GO and Fe3O4 NCs.36 Wang et al. fabricated GO/MnO2 nanocomposites via a simple chemical route in a water-isopropyl alcohol system and then demonstrated the composite can act as electrode material for supercapacitors.38 Qin et al. fabricated reduced GO/MnO2 composite electrodes by in situ anodic electrodeposition.40
The aforementioned hybrids have shown to act as promising electrode materials for supercapacitor applications. However, all of these methods used GO or reduced GO as the precursor, and they are known to possess high densities of irreversible structural defects in their lattices. Another drawback of these potential supercapacitor materials is that the particle size and loading density of attached NPs cannot be precisely controlled. Moreover, these synthetic techniques require multiple complicated synthetic steps and additionally require the use of surfactants. Qian et al. developed a one-step synthetic procedure to both produce the transition metal oxide NCs and attach the NCs to the graphene surface.41 High-quality graphene hybrid with attached magnetite (Fe3O4) NCs were readily prepared using a simple solvothermal process. Iron (III) acetylacetonate (517003) and expanded graphite were employed as precursors, and ethanol was used as a safe and harmless reaction medium. No surfactant was involved in the preparation of these nanophase composite materials. Experimental results demonstrated that this simple and environmentally friendly chemical process could be extended to hybridize other metal oxide NCs, such as Mn3O4 and CoO. TEM analyses indicated that the particle size and coating density of Fe3O4 and Mn3O4 could be readily tailored by varying reaction time, as shown in Figure 1.
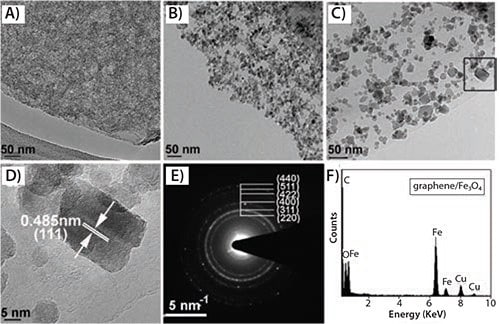
Figure 1.TEM analysis of graphene/Fe3O4 composites prepared by solvothermal reaction at 180 °C at varying reaction times of 4 h (A), 8 h (B), and 16 h (C); D) HRTEM image of boxed area of (C); E) the corresponding SAED pattern; F) typical EDS pattern of the attached Fe3O4 NCs.
The electrochemical performance of graphene/Mn3O4 (803723), graphene/Fe3O4 (803715) and graphene/CoO composites as supercapacitor anode materials was also investigated. These hybrids were found to exhibit enhanced capacitance compared to that of pristine graphene and pure NCs, and have high current density while maintaining long-term cycling stability (Figure 2).
Hybridization of Graphene with Noble Metals and Alloys for Energy Conversion Devices
Direct methanol fuel cells (DMFCs) are becoming attractive competitors to traditional fuels for transportation and electrical power generation—especially for mobile and portable applications—due to their exciting performance advantages.42–44 Currently, XC-72 carbon black is the most widely used carbon support for fuel cell catalysts because of its good balance between electronic conductivity and high surface area. However, commercial carbon-supported platinum (Pt/C) fuel cells have serious deficiencies, including the slow rate of oxygen reduction reaction (ORR), the high cost of platinum, the cross-over of methanol from the anode to the cathode through the proton exchange membranes, the vulnerability of the reaction to be poisoned by carbon monoxide (CO), and the rapid loss of catalytic activity caused by the existence of halide ions, as well as catalyst particle aggregation and deformation.45,46 As a result, the lifetime of such a fuel cell is rather poor. The introduction of a second, less expensive transition metal such as Fe, Ni, Co, Cr, Pd, Ru, or Bi to form Pt-based alloys has proven to enhance electrocatalytic activity for ORRs, taking advantage of the increased Pt d-band vacancy and more favorable Pt-Pt interatomic distance in comparison with using Pt alone.47–49 In order to maximize the catalytic activity of Pt and to minimize expensive Pt material consumption, it is necessary to prepare Pt NCs with ultrafine sizes. Obviously, the highly accessible surface area and the number of edge and corner atoms of the small NCs would greatly improve the catalytic activity. To avoid detrimental aggregation of the small NCs, the existing methods of synthesizing small NCs rely on surfactants50 and ligands51 to stabilize the NCs. The drawback of the presence of surfactants in the resulting product is the seriously decreased electrocatalytic performance. Therefore, selecting an ideal substrate, then hybridizing it with uniformly dispersed Pt NCs and Pt-M alloys—but without the use of a surfactant or stabilizer—is urgently needed for the advancement of DMFCs.
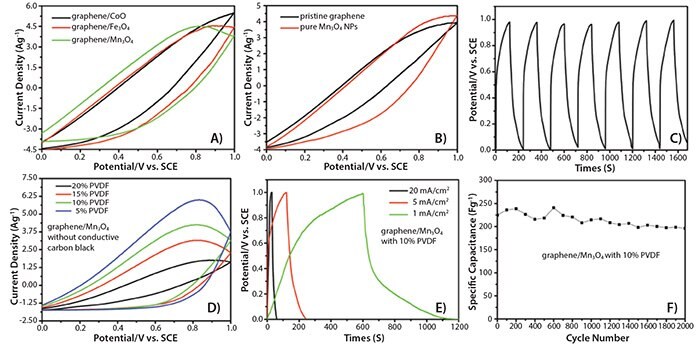
Figure 2.A) Cyclic voltammetry (CV) curves of graphene/Fe3O4 (803715), graphene/Mn3O4 (803723) and graphene/CoO composites, at a scan rate of 10 mV/s in 0.5 M NaCl(aq). B) CV curves of pristine graphene and pure Mn3O4 NPs at a scan rate of 10 mV/s in 0.5 M NaCl(aq). C) Galvanostatic charge-discharge curve of a graphene/Mn3O4 composite at a current density of 2 A/g in 0.5 M NaCl(aq). D) CV curves of graphene/Mn3O4 composites without any conductive carbon black but with different ratio of PVDF as binder, at a scan rate of 10 mV/s in 0.5 M NaCl(aq). E) Galvanostatic charge-discharge curve of a graphene/Mn3O4 composite at a current density of 1 mA/cm2, 5 mA/cm2 and 20 mA/cm2 in 0.5 M NaCl(aq). F) Long-term cycling performance of a graphene/Mn3O4 composite with 10 wt% PVDF.
The emergence of graphene material has enabled a new opportunity to utilize the 2D graphitized planar structure as a substrate for growing and anchoring noble metal NCs and alloy NCs, including Pt,52–55 Pd,56,57PtPd,58 and PtRu59 NCs for high-performance electrocatalytic devices. Jalan et al. suggested that the enhanced electrocatalytic activity was due to the contraction of the Pt-Pt interatomic distance by adding a smaller transition metal atom.60 Ross et al. commented that the roughening of the Pt surface due to the addition of the transition metal could account for the ORR improvement.61,62 Mukerjee et al. explained this by an increase in Pt d-band vacancies and a more favorable Pt-Pt mean interatomic distance.63,64 Most of these methods selected H2PtCl6 (254029, 520896) and GO (763705, 777676) as the precursors, which results in rapid loss of catalytic activity. Qian et al. developed a simple, low-cost and environmentally benign process to hybridize exfoliated few-layer graphene sheets with nanocrystalline Pt (Pt/graphene, Prod. No. 803693) and Pt-based alloys (PtPd/graphene (803758) and PtCo/graphene (803766)).65 TEM images indicated that both the resultant single-Pt NCs (Figure 3) as well as alloy (Figure 4) were uniformly distributed on the graphene surface and the loading density easily controlled by the reaction times. Most important, no surfactant and no halide ions were involved in the whole reaction.
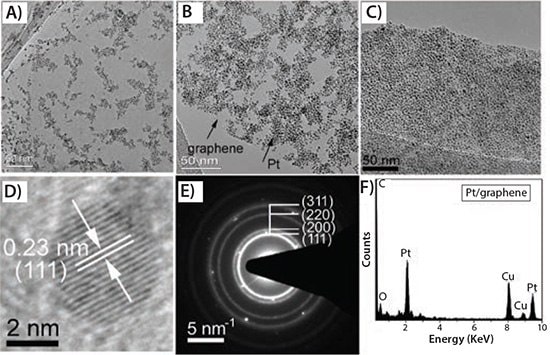
Figure 3.TEM analysis of Pt/graphene hybrid (803693) prepared by a solvothermal reaction at 115 °C at varying reaction times of 6 h (A), 12 h (B), and 18 h (C); D) HRTEM micrograph of Pt/graphene hybrid; E) the corresponding SAED pattern; and F) EDX spectrum of deposited Pt NCs.
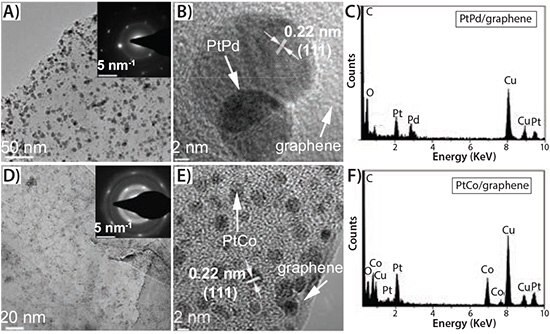
Figure 4.TEM analysis of both PtPd/graphene ( 803758) (A–C) and PtCo/ graphene (803766) (D–F) hybrids prepared by a solvothermal reaction at 115 °C for 6 h. A) TEM image of graphene sheet with attached PtPd alloys NCs and corresponding SAED pattern (inset). B) HRTEM micrograph of PtPd/graphene hybrid. C) EDX spectrum of the deposited PtPd alloy NCs. D) TEM image of graphene sheet loaded with PtCo alloys NCs and corresponding SAED pattern (inset). E) HRTEM micrograph of PtCo/graphene hybrid. F) EDX spectrum of the deposited PtCo alloy NCs.
In comparison to commercial Pt/C catalysts, high-quality graphenesupported Pt, PtPd, and PtCo NC hybrids as electrocatalysts demonstrated excellent electron transport, improved efficiency toward methanol oxidation, and improved tolerance to CO poisoning, as well as long-term stability (Figure 5).
Hybridization of Graphene with TiO2 for Energy Production Devices
Since hydrogen is commonly regarded as the ultimate clean fuel, the production of hydrogen with solar power plays an important role in clean and renewable energy systems.66,67 Among all solar-to-hydrogen conversion methods, direct water splitting by a photocatalyst is the most convenient process.68 Anatase TiO2 (637254, 232033 and 248576), a wide-band-gap semiconducting material, is widely known for use in photocatalysts due to its unique optical and electronic properties. Under UV illumination, electrons are excited from the valence band to the conduction band, forming electron-hole pairs. The purpose of the graphene substrate is to achieve the photocatalytic activity by separating the electron-hole pair, but leaving the hole on the TiO2 to form the radical, as shown in Figure 6. The photo-generated electron-hole pairs of the TiO2 have a flash recombination time on the order of 10–9 s, while the time of chemical interaction of TiO2 with adsorbed pollutants is in the range of 10–8–10–3 s.69,70 In addition, the photocatalytic activity of TiO2 is strongly dependent on morphology71,72 and particle size.73 Experiments have generally shown that reducing pure TiO2 particle size would increase photocatalytic activity by decreasing the electron-hole recombination rate in the bulk of the crystal. Once the particle size falls below ~15 nm, recombination rates at the surface become the dominant interaction; decreasing the particle size beyond this point leads to a decreased photocatalytic activity.74 Utilizing the charge separation aspect of TiO2/graphene composites, it is hypothesized that this surface recombination effect can be mitigated, allowing further photocatalytic enhancement through particle size reduction beyond this 15 nm size limit. Graphene/TiO2 hybrids have attracted particular interest for this reason and have been shown to provide drastic increases in photocatalytic and photovoltaic performance when compared to lone TiO2 catalysts.75,76
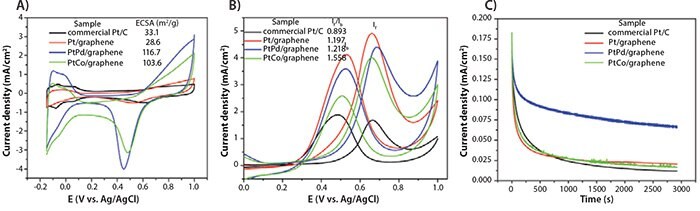
Figure 5.A) Cyclic voltammograms of commercial Pt/C (black), Pt/graphene (red), PtPd/graphene (803758) (blue) and PtCo/graphene (803766) (green) in N2-saturated 0.5 M HClO4 electrolyte, at a scanning rate of 50 mV/s. B) Cyclic voltammograms of commercial Pt/C (black), Pt/graphene (red), PtPd/graphene (blue) and PtCo/graphene (green) in 0.5 M CH3OH/0.5 M HClO4 electrolyte, at a scanning rate of 50 mV/s. C) Chronoamperometric curves recorded at 0.65 V (vs Ag/AgCl) of the electrocatalysts in 0.5 M CH3OH/0.5M HClO4 electrolyte for 3,000 seconds.
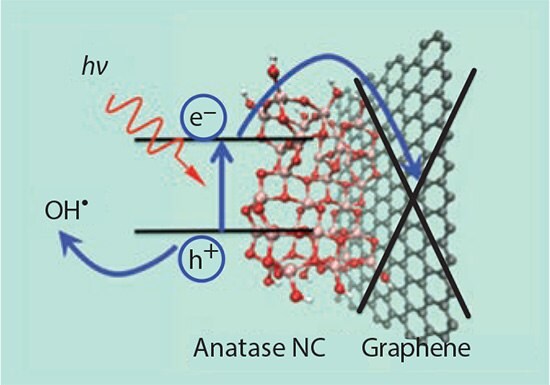
Figure 6.Schematic of the separation of a photoexcited electron-hole pair in a TiO2 NC.
TiO2 NCs have long been studied due to their potential photocatalytic applications in water purification and hydrogen-energy production.77–79 Both theoretical prediction and experimental results indicate that (001) facets of anatase TiO2 are much more reactive than other thermodynamically stable facets.80–83 Since the pioneering work by Lu et al. on the synthesis of micrometer-sized anatase crystals with a large percentage of (001) facets,80 there has been remarkable interest in the controlled synthesis of anatase crystals with varied percentages of exposed (001) facets, such as truncated tetragonal bipyramids and square sheets.82–85 Hybridizing shape-controlled TiO2 NCs on the surface of graphene sheets may not only favor the dispersion of NCs, but also contribute to the improvement of photocatalysis due to the unique electron mobility. Zhang et al. was the first to prepare a chemically bonded TiO2 (P25)-graphene composite photocatalyst by hydrothermal reaction.86 Since then, many efforts using the synthesis of GO/TiO2 composites have been made in order to increase the efficiency of photocatalysis;87–89 however, none of these efforts used exfoliated crystalline graphene as a precursor. Recently, Qian et al.90 successfully hybridized highly conductive graphene with nanocubic TiO2 NCs. These composite materials clearly show a lattice spacing of 0.35 nm corresponding to the (101) plane of anatase TiO2, as can be seen in Figures 7A–B. Considering that anatase TiO2 adopts a tetragonal structure with lattice parameters a = b = 0.377 nm and c = 0.950 nm, the square surface in the crystal structure can be assigned to (001) facets.
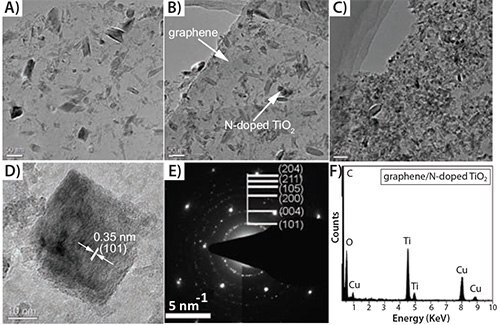
Figure 7.TEM analysis of N-doped TiO2/graphene prepared at low temperature of 180 °C at varying reaction times of A) 7 h, B) 14 h, and C) 21 h; D) HRTEM image of deposited N-doped TiO2 NCs; E) corresponding SAED pattern; F) typical EDX pattern of deposited N-doped TiO2 NCs.
Conclusion
The fabrication of novel graphene-based composites by combining high-quality graphene with various metal and metal oxide NCs has proven to be a very promising approach for developing improved clean energy devices. These new graphene-based metal and metal oxides are expected to have an impact in three categories within the clean energy arena: energy storage (supercapacitors), energy conversion (fuel cells), and energy production (hydrogen generation via water splitting). Once technological and performance issues are fully resolved, these nanocomposites have the potential to be manufactured on an industrial scale and to help address significant global economic andenvironmental challenges.
Related Materials
References
To continue reading please sign in or create an account.
Don't Have An Account?