Advances in Li-Metal Fluoride Battery
Rajesh Pathak1, Ke Chen1, Yue Zhou1, Qiquan Qiao1,2
1South Dakota State University, 2Syracuse University
Material Matters™, 2020, 15.2
- Introduction
- Structural Design of the Cathode
- Stabilization of Li Metal Anode
- Selection of Battery Components and Testing Conditions
- Conclusions and Future Outlook
Introduction
Conventional lithium-ion batteries (LIBs) utilize intercalationtype cathode materials, including layered LiCoO2 (LCO), spinel LiMn2O4 (LMO), olivine LiFePO4 (LFP), and layered LiNixMnyCozO2 (NMC).1–2 However, these intercalating chemistries are rapidly approaching their practical achievable capacity and are currently the most significant limitation of the energy density of most commercial batteries. LIBs are the preferred energy storage device for portable electronics, electric vehicles, and grid-level energy storage but batteries with higher specific power/energy density, longer cycle life, and lower costs are still needed.3–6 Li metal anodes combined with conversion-type lithium cathode chemistries such as lithium-metal fluoride (Li-MF) have shown tremendous potential to fulfill such requirements, owing to their higher theoretical potentials (3.55 vs. Li/Li+ for CuF2) and higher gravimetric and volumetric capacities (713 mAh g-1 and 2196 mAh cm-3 for FeF3).7 In addition to CuF2 and FeF3, other metal fluorides such as FeF2, CoF2, and NiF2 exhibit both higher theoretical discharge potential and higher volumetric capacity enabled by more than one electron transfer per transition metal.8 The multiple reversible redox electrochemical conversion reaction is shown in equation 1 below.8 Besides, both fluorine and metal elements such as Fe, Cu are naturally abundant.
mnLi+ + MnXm + mne- ↔ mLinX + nM0 (1)
Here, “M” stands for the transition-metal ions, “X” denotes fluoride, “m” and “n” indicate the amount of lithium uptake. Despite attractive features, multiple limitations have hindered the practical applications of MF cathodes. These barriers include low electronic conductivity, undesired side reactions with electrolytes, and the volume change during charge/discharge.9 These features have led to poor reversibility of capacity or low coulombic efficiency, large voltage hysteresis, and quick capacity degradation upon cycling. To counter these effects, researchers have made numerous efforts to regulate the MF cathode based upon three principles: (1) structural design of cathodes, (2) stabilization of Li metal anode, and (3) selection of battery components and testing condition.
The desire to revitalize research on the Li-MF batteries has spawned successful efforts to understand and solve the challenges to provide novel concepts towards achieving high practical, specific energy, and long cycle-life. This review explores the most important concepts in designing electrochemically stable microstructures that possess wide Li-ion insertion channels and an ideal nano-morphology. Furthermore, this article evaluates the development of more suitable electrolytes by optimizing the concentration, adding additives and fillers, engineering high modulus solid electrolytes and polymer electrolytes, and ex-situ formation of artificial solid electrolyte/electrode interface (ASEI) in order to stabilize the Li metal anode. Additionally, this review examines the optimization and modification of the battery components and the utilization of suitable parameters and conditions during battery testing that can offer a complimentary pathway in improving the performance of the MF batteries.
Structural Design of the Cathode
Precise control over crystallization, effective prevention of particle growth and agglomeration, and establishing ideal nano-morphology of the cathode material (including wide Li-ion insertion channels) can all contribute toward improved transport and reaction kinetics of MF cathodes. However, scientists still face challenges in improving electronic conductivity, since conventional architecture based on composites or encapsulating nanosized MF in a three-dimensional (3D) carbon network still face challenges such as sluggish reaction kinetics and inhibiting the side reactions. Both binary MFs such as CoF2 and ternary MFs such as NiyFe1-yF2 have shown great promise. Similarly, FeF3 or FeF2 shows high reversibility and low cost, and CuF2 shows a high theoretical potential of 3.55 V and a high gravimetric energy density of 1874 Wh/kg.10 However, FeF2 has a low working potential (2.60 V) and CuF2 is irreversible during charge/ discharge cycles. The irreversibility of CuF2 is due to the high diffusivity of Cu ions, leading to phase-separated nano metallic Cu during discharge and loss of active material due to the transport of cuprous ions during charge.
On the cathode side, substantial efforts have been made to alleviate challenges associated with active metal dissolution, electrolyte degradation, electrode volume restriction, and selective fluorine-ion percolation. Wu et al. reported a FeF3@C composite with a 3D architecture comprised of honeycomb walls and 3D hexagonal channels. The scanning electron microscopy (STEM) and high-resolution transmission electron microscopy (HRTEM) of 3D honeycomb FeF3@C composite are shown in Figure 1A. The 3D porous framework and hexagonal-like channels of carbon simultaneously enable fast electron transfer and Li-ion transport, respectively.9 Within the structure, the honeycomb channels range from hundreds of nanometers to a few micrometers in size. The walls of those honeycomb channels are embedded with isolated FeF3 nanoparticles of sizes ranging from 10–50 nm.
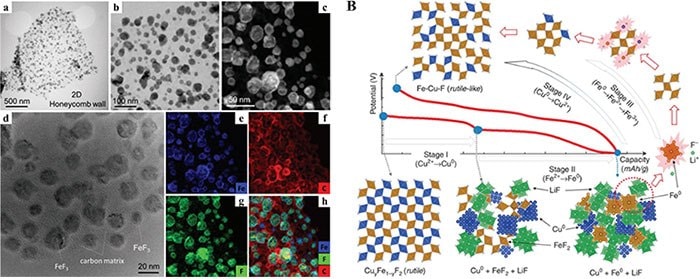
Figure 1.A) STEM and HRTEM images of 3D honeycomb carbon and FeF3 composite: (a,b) STEM, (c) HRTEM, (d) high-resolution STEM and (e-h) the corresponding elemental of iron (Fe), carbon (c), fluorine (F) and their combined mapping from (d).9 B) The reaction pathway of ternary CuyFe1-yF2. The reduction of Cu and Fe during initial discharge follows Stages I and II, while the oxidation of Fe and Cu follows III and IV.7
As a result, this FeF3@C cathode exhibited a small voltage hysteresis of ~ 0.30 V at 1C with the following properties: a mass loading of 5.3 mg cm-2, 0.25–0.28 V at C-rate between C/2 and 10C with a mass loading of 1.0 mg cm-2, excellent rate capabilities up to 100C, almost no capacity fading up to 200 cycles, and capacity retention of ~85% after 1000 cycles.
Wang et al. found a surprisingly small overpotential (<150 mV) by preparing solid-solution ternary MF through the substitution of Cu into the Fe lattice.7 Here, the incorporation of Cu facilitates a collaborative redox reaction that leading to the reversible reaction Cu2+↔Cu0. The description of the reaction mechanism and phase evolution is demonstrated in Figure 1B. This cation substitution provided a new pathway for customizing the irreversibility issues in MF cathodes. During stages I and II the reduction of Cu and Fe occurs. During stage III, the reformation of the rutile-like Cu-Fe-F phase occurs. During higher potential (stage IV), most Cu transform back to rutile structure but some amount of Cu gets dissolved in the electrolyte or is irreversible, which implies that the final phase could have Cu-deficiency. Later on, to improve the reversibility of CuF2, Omenya, et al. studied the presence of Fe in Cu1-yFeyF2.10 The reversibility of Cu0.5Fe0.5F2 is due to the presence of Fe, which shows a reversible conversion and intercalation redox reaction in the low and high voltage regions, respectively.10
Further, the anion’s and cation’s co-substitutions (doping of cobalt and oxygen) into nanorod iron fluoride can thermodynamically lower the working potential but improves the reversibility of intercalation reaction.11 Various strategies have been proposed to prevent the dissolution of the metal ions that causes degradation of the cathode and sluggish Li-ion transport. Potential solutions include 1) deposition of a cathode protective thin film using high-quality film uniformity and excellent conformality over high-aspect-ratio; 2) a core-shell nanostructure with an inert, thin shell of LaF3 as an ASEI with Cu as a core; and 3) FeF2 infiltrated into carbon mesopores.12–14 Additionally, the in-situ formation of cathode SEI with a suitable choice of the liquid and solid electrolyte offers another approach to stabilize the MF-cathodes. For example, Xiao et al. obtained a capacity of 570 mAh g-1, outstanding cycling stability, and more than 90% capacity retention at the charge/discharge rate of C/20.1 Scientists accomplished this feat thanks to the formation of stable SEI and prevention of the dissolution of metal ions by the use of single-crystalline, monodisperse iron (II) fluoride nanorods and ionic liquid (1M LiFSI/Pyr1,3FSI).
Stabilization of Li Metal Anode
Scientists have made substantial efforts to deposit Li metal dense and reversible manner, including designs that include a suitable liquid or solid electrolyte, development of stable Li host materials, as well as the development of an ASEI. The choice of Li salt, a salt concentration, and composition of the solvent determines the nature of the in-situ formed cathode/ anode SEI. The design of suitable liquid electrolytes results in improved structural stability, flexibility, and compatibility between the anode and electrolyte interface. Such electrolytic solutions contain a combination of LiFSI-DME, acyclic organic carbonate solvents, a mixture of ADN-FEC solvent, electrolyte additives, and nitriles.13–15 To further stabilize the Li metal anode, use of a Li ion-conducting coating, solid polymer electrolyte, and a high fluorine anion conducting tysonite-type La0.9Ba0.1F2.9 have been reported.1,6,17 The development of Li host materials and nanostructured scaffolds is another approach to accommodate Li. The lightweight nanostructure with lithiophilic sites can accommodate sufficient Li and facilitate the uniform Li deposition, leading to improved cycling performance and lower voltage hysteresis.5,18 In addition to that, the development of ex-situ ASEI with high chemical and mechanical stability, high ionic conductivity and Young’s modulus, control on their composition, and thickness can lead to dendrite free Li deposition and stable SEI.3–4 This leads to the control of both Li and liquid electrolyte consumption and inhibits the formation of fragile and unstable, unfavorable, overly thick SEI. Figure 2 shows the schematic illustration of the development of SEI by drop-casting SnF2 on the Li metal electrode. With the displacement reaction, SnF2 and Li react to form an ASEI composed of Li-Sn alloy, LiF, and electrochemically active Sn beneficial for dendrite-free Li deposition. Moreover, the stable SEI prevents the reprecipitation of the dissolved metal ion.
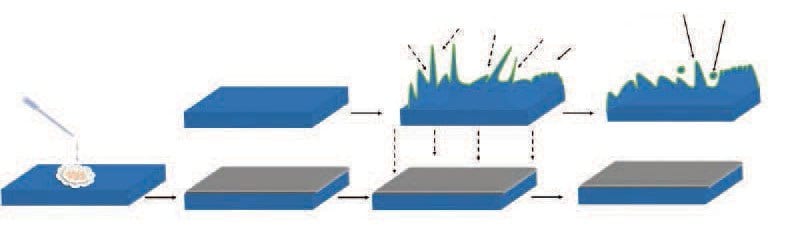
Figure 2.Schematic representation of Li plating/stripping in A) bare Li and B) SnF2 pre-treated Li.3
Selection of Battery Components and Testing Conditions
Besides the development of advanced 3D cathode structure and stabilization of Li metal anode, the cell design principle (which consists of a selection of battery components), their modifications, and testing conditions can offer a complimentary pathway in improving the performance of the MF batteries. The use of suitable carbon additives or binders and modifying the separator with lithiophilic coatings has the potential to lead to the reversibility of MF cathodes. In addition to this, the battery testing condition, such as defining the preferred charge/ discharge current density and the charge/discharge voltage limit, can also reduce the dissolution of metal and/or degradation of electrolyte. The increase in the temperature during cell testing could prove beneficial to form stable SEI and suppress Li dendrite growth that leads to enhanced rate capability and capacity utilization.19
Conclusions and Future Outlook
Li-MF batteries may be able to satisfy the fast-growing demand for lightweight, high-capacity, and high-energy-density storage. Momentous research efforts are underway that could bring safety, low-cost, and reversibility of the capacity, leading to the development of conversion-type Li-MF batteries that allow storage of nearly two times more volumetric energy density and nearly three times gravimetric energy density, respectively, compared to conventional electrodes. This review summarizes the efficient approaches that have addressed the prevailing electrochemical instabilities and capacity irreversibility in MF cathodes.
In addition to the major issues covered in this review, future studies are likely to continue to focus on the essential areas of materials discovery and advanced interfacial characterization. For example, the discovery of novel computational and experimental techniques can help to identify lightweight and low-cost cathode structures to further address poor electronic conductivity, volume expansion, and dissolution of the active metal. Atomic-scale characterization and modeling techniques will help us to better understand the electrode/electrolyte interfacial chemistry required. The most effective and efficient technologies must be developed for use in practical cell application formats with a high-MF cathode mass loading, lean electrolyte, and limited ratio of the areal capacity of the negative electrode (Li) to the areal capacity of MF positive electrode (N/P). Furthermore, reproducible protocols and standards for the synthesis of the cathode structure, formation of in-situ or ex-situ anode/cathode SEI, electrolyte optimization, selection of battery components, battery fabrication, and cycling metrics are crucial for the successful deployment Li-MF battery technology.
Acknowledgments
This work has been supported by NSF MRI (1428992), NASA EPSCoR (NNX15AM83A), SDBoR Competitive Grant Program, SDBoR R&D Program, and EDA University Center Program (ED18DEN3030025).
Conflict of Interest
The authors declare no competing interests.
Materials
To continue reading please sign in or create an account.
Don't Have An Account?