Dispensette® Testing Instructions (SOP)
Read more about
- 1. Introduction
- 2. Preparation for Testing and Visual Examination
- 3. Required Equipment for Testing
- 4. Gravimetric Test
- 5. Evaluation of Gravimetric Test Results
- 6. Test
- 7. Calibration Service From Brand®
- 8. EASYCAL™ Software – Advanced Calibration Technology
- 9. DAkkS-Calibration Service for Volumetric Instruments at BRAND®
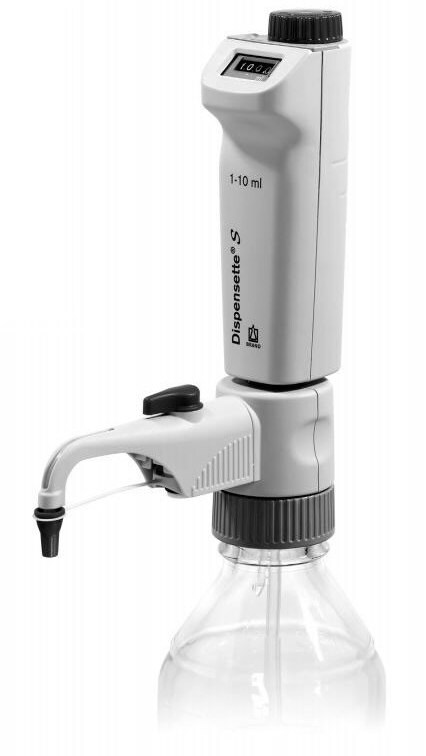
1. Introduction
The standard ISO DIS 8655 describes both the design and the testing of the bottle-top dispenser. The following Testing Instructions describe how to apply the ISO standard in practice.
We recommend a testing every 3-12 months. This interval may be adjusted to individual requirements. For example, when working very frequently or when using aggressive media, the instrument should be tested more frequently.
These Instructions may also be used as a basis for the supervision of testing devices to DIN EN ISO 9001, DIN EN ISO 10 012 and DIN EN ISO/IEC 17 025.
For the regular examinations required by DIN EN ISO 9001, DIN EN ISO 10 012, DIN EN ISO/IEC 17 025 and the GLP Guidelines, BRAND® additionally provides a calibration service. Your instrument will be returned within a few days together with a test report. For more detailed information, please contact your labware supplier.
2. Preparation for testing and visual examination
2.1. Type and Serial Number
- Determine instrument type and nominal capacity. ⇒ Enter/ check in Test Record (1).
- Read Serial Number (embossed at valve block). ⇒ Enter number in Test Record (1).
- Read customer’s identification, if present. ⇒ Enter identification in Test Record (1).
2.2. Minimal Configuration Dispensette®
- Dispenser ⇒ Use only manufacturer’s original parts.
- Discharge tube
- Filling tube
- Mounting tool for valves
2.3. Cleaning
- Rinse instrument with cleaning solution. Then rinse the instrument again several times wich was used. ⇒ Select suitable cleaning solution according to the medium with distilled water.
- Wipe off the exterior of the Dispensette®.
⇒ Unscrew piston and lift it out completely following the instructions of the operating manual. Remove desposits out glass cylinder and piston.
2.4. Visual Examination (Damage, Leakages)
- Housing ⇒ Enter fillings in Test Record (2).
- Discharge tube
- Filling tube
- Controls
- Leakage
2.5. Functional Test
- Screw the Dispensette® on a bottle filled with distilled or deionised water (according to ISO 3696, at least quality 3).
- Priming (see Operating Manual). ⇒ A few bubbles up to 1 mm in the glass cylinder are permissible.
- Check the volume adjustment and that the dispensing piston moves freely. ⇒ The dispensing piston must slide smoothly in the dispensing cylinder.
- Result ⇒ Enter findings into Test Record (3)
If there is a malfunction of the instrument (e.g., piston difficult to move, sticking valves or leakage) please consult the "Troubleshooting" section of the operating manual.
3. Required Equipment for Testing
- Dispensette®
- Bottle (at least 500 mL) filled with distiled or deionised water (according to ISO 3696, at least quality 3, room temperature). ⇒ Match temperature of water and room.
- Recipient (e.g., Erlenmeyer flask, narrow-mouth) filled with some water. ⇒ Bottom of vessel should be covered.
- Thermometer with a measuring error of maximum: ± 0.2 °C
- Place the instrument into the testing room for at least 1 hour (unpacked!). ⇒ Allow instrument to adjust to room temperature.
- Balance
Traceability of Test Results to National Standards
Through the use of calibrated testing devices (balance and thermometer), the requirement of DIN EN ISO 9001, DIN EN ISO 10012 and DIN EN ISO/IEC 17025 to refer the test to the national standard is fulfilled. The calibration of the balance e.g. can be carried out either by DAkkS calibration or official certification of the balance, or by calibrating the balance with appropiate weights that are traced to the national standard. The calibration of the thermometer can also be carried out by DAkkS calibration or official certification, or by a comparison with thermometers that are traced to the national standard (under defined conditions).
4. Gravimetric test
- Determine temperature of the water for testing. ⇒ Enter temperature into Test Record (4).
- Set instrument to nominal volume.
- Dispense some liquid into the separate vessel. Wipe off the drop on the discharge tube against the wall of the recipient.
- Place recipient upon the balance. Tare the balance.
- Place recipient under the discharge tube.
- Pull up the piston as far as it will go. ⇒ Move slowly and steadily.
- Push the piston all the way down. ⇒ Move slowly and steadily.
- Wipe dispensing tube at the receiving vessel.
- Place receiving vessel upon the balance. Write down the value. ⇒ Enter weighing value into the Test Record (5).
- Tare the balance again.
- Repeat points 2 to 10 another ten times.
- Then carry out ten more weighings each by dispensing 50% resp. 10% of the nominal capacity.
5. Evaluation of gravimetric test results
The values obtained by weighing during the gravimetric test are only the mass values of dispensed volume without correction of air buoyancy. In order to obtain the actual volume, an adjustment calculation to account for water density and air buoyancy must be carried out. To facilitate your calculations and evaluations, we recommend the use of the Windows-compatible calibration software EASYCAL™ from BRAND®.
The following calculations must be carried out:
1. Mean weighing values:
(Example for ten weighing values)

2. Mean volume:
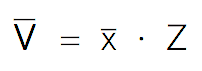
⇒ For factor Z (Table 4)
⇒ Enter value into Test Record (6a).
3. Standard deviation volume:

⇒ For factor Z, Table 4
⇒ Enter value into Test Record (6b)
4. Accuracy:
![accuracy_eq Accuracy equation. Mathematical formula for calculating percentage deviation, represented as A[%], which equals the difference between V measured and V nominal, divided by V nominal, all multiplied by 100.](/deepweb/assets/sigmaaldrich/marketing/global/images/technical-documents/protocols/analytical-chemistry/wet-chemical-analysis/accuracy_eq/accuracy_eq.png)
⇒ Enter value into Test Record (6c)
5. Coefficient of variation:
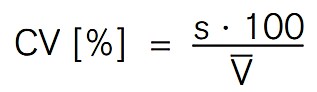
⇒ Enter value into Test Record (6d)
Comparison actual/nominal values:
Use the error limits per Table 5 and 6, or define your own error limits. ⇒ Enter values into Test Record (6e, f).
Result
If calculated values A [%] and CV [%] are smaller than or equal to the error limits, the instrument is in good working order.
If the calculated values are larger than the error limits:
- Verify if the above instructions have been carefully followed step by step.
- Observe the suggestions under "Troubleshooting" in the Operating Manual.
- Calibrate the Dispensette® according the instructions in the Operating Manual.
If these measures are not successful, we offer you the possibility to have your instruments calibrated by the BRAND® Calibration Service.
6. Test
10 single measurements per test volume according to DIN EN ISO 8655. For definition of A, CV and s see sample calculation chapter 5. For checking of partial volumes the values for A [%] and CV [%] which are related to the nominal volume have to be converted.
For calibration, the error limits to be observed by the operator must be individually defined by the user. For this purpose, the following methods can be applied:
- If required by the application and if the optimized conditions for measuring are present, the error limits in Table 5 can also be expected in the case of used volumetric instruments in good working order.
- In analogy to the German regulations for official testing, it is also admissible to apply the limits which are typical for practice. These practice limits correspond to double the limits for official testing. In this case, the values found in Table 5 should be doubled.
- The user may also define his own individual error limits corresponding to his particular application, and apply these tolerances for the calibration of his instrument.
The above procedures fulfil the requirements of DIN EN ISO 9001, DIN EN ISO 10012 and DIN EN ISO/IEC 17025.
7. Calibration Service from BRAND®
BRAND® offers a full service including calibration and adjustment of Brand- and foreign instruments as well as maintenance and repair if necessary - only for BRAND®- instruments. This saves money and adds the benefit of an independent review organisation for the calibration of the instruments. Further information and the order form for repair- and calibration service are found on www.brand.de.
7.1. Range of Instruments Covered
- Piston-operated pipettes (single- and multichannel)
- Bottletop dispensers
- Piston burettes (bottle-top burettes)
- Hand dispensers
7.2. Testing According to DIN EN ISO 8655
At BRAND®, a team of qualified staff, working in temperature and humidity controlled rooms using the most modern balances and calibration software, calibrates Liquid Handling instruments, regardless of their make, according to DIN EN ISO 8655.
Instruments with adjustable volumes such as HandyStep® electronic, Transferpette®, Transferpette® S, Transferpette® electronic, Transferpette®S -8/-12, Transferpette® S -8/-12. Transferpettor or Dispensette®, Digital Burette or Titrette® are tested at nominal volume, and at 50%, 10% or 20% of nominal volume.
To document the results, a detailed test report is compiled.
The BRAND® Calibration Service offers:
- Calibration of Liquid Handling instruments, regardless of their make
- Detailed calibration certificate
- Return of instrument within a few working days
- Cost-efficient handling
8. EASYCAL™ Software – advanced calibration technology
8.1. For Liquid Handling Instruments and Glass or Plastic Volumetric Instruments
EASYCAL™ simplifies the tedious task of calibrating liquid handling instruments and glass or plastic volumetric instruments to DIN EN ISO 9001, DIN EN ISO 10012, DIN EN ISO/IEC 17025 and GLP standards. The procedures are outlined step-by-step, and all calculations are performed automatically. Reports are generated to document the calibration. All you need is an analytical balance, a PC Windows® 98/2000, NT (SP6), XP, Vista, 7, printer (optional) and EASYCAL™ software.
- Suitable for instruments from all manufacturers.
- Specifications of many instruments preloaded.
- Testing according to ISO 4787, ISO 8655, etc.
8.2. Data Entry
- Connect PC and balance (optional), then start the EASYCAL™ software.
- 100 common balances are preprogrammed for ease of installation.
8.3. Documentation
The calibration certificate contains all important test data on one page.
9. DAkkS-Calibration Service for Volumetric Instruments at BRAND®
9.1. DAkkS – Deutsche Akkreditierungsstelle GmbH and DKD
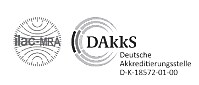
The German Calibration Service (DKD) was founded in 1977 as a joint task of state and economy and constitutes the link between the measuring equipment in industrial and research laboratories, testing institutions and authorities and the national standards of the PTB (the German Institute of Physics and Metrology). It effectively supplements the existing verification system which serves above all the purposes of consumer protection. Based on the legal requirements the DKD Accreditation was successively transformed to the DAkkS Accreditation (Deutsche Akkreditierungsstelle GmbH), starting from 2010. BRAND® has been accredited by the DAkkS since Apr. 23, 2013, with the certificate number D-K-18572-01-00.
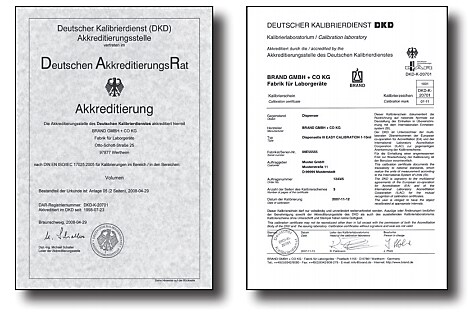
9.2. DAkkS-Calibration Certificate and Calibration Symbol
The DAkkS-Calibration Certificate documents officially on a high level the traceability of measuring results to national and international standards and to international SI-units, as required by standards as DIN EN ISO 9001 and DIN EN ISO/IEC 17025 for monitoring of measuring devices.
DAkkS-Calibration Certificates are issued when calibrations of an accredited laboratory are requested, when high level calibrations are necessary, when national and international standards are demanded and when reference instruments have to be calibrated.
9.3. DAkkS – A member in the International Accreditation Network
DAkkS is a member of the International Laboratory Accreditation Cooperation (ILAC), the highest level international institution for laboratory calibration, and is a signatory to the MRA – Mutual Recognition Agreements.
The accreditation bodies that are signatories to the ILAC mutual recognition agreements (MRAs) recognize their mutual equivalence, and the equivalence of the calibration certificates issued by those same signatories. Likewise, signatories are obliged generally to promote and recommend recognition of the calibration certificates of other signatories (excluding factory calibration certificates).
The DAkkS is a member of the EA (European Co-operation for Accreditation), which again is a member of the ILAC (International Laboratory Accreditation Cooperation). A multilateral agreement assures obligatory recognition of the DakkS calibration certificate in a variety of countries.
9.4. DAkkS-Calibration Laboratory at BRAND®
In 1998 a calibration laboratory for volumetric instruments at BRAND® has been accredited by the German Calibration Service according to DIN EN ISO/ IEC 17 025. Our calibration laboratory is therefore authorized to issue DAkkS-Calibration Certificates (in several languages) for the volumetric instruments listed below. Furthermore we offer adjustment and – for BRAND® Liquid Handling instruments – repair and maintenance.
For ordering information on DAkkS-Calibration Certificates for volumetric instruments please consult our General Catalog.
9.5. Volumetric instruments for which BRAND® issues DAkkS Calibration Certifcates
BRAND® calibrates the following volumetric instruments (new or already in use and regardless of their make):
- Piston-operated pipettes, from 0.1 µL to 10 mL
- Multichannel piston-operated pipettes, from 0.1 µL to 300 µL
- Piston-operated burettes, from 5 µL to 200 mL
- Dispensers, Dilutors, from 5 µL to 200 mL
- Volumetric instruments of glass, calibrated to contain (TC, In) from 1 µL to 10000 mL
- Volumetric instruments of glass, calibrated to deliver (TD, Ex) from 100 µL to 100 mL
- Volumetric instruments of plastic, calibrated to contain (TC, In) from 1 mL to 2000 mL
- Volumetric instruments of plastic, calibrated to deliver (TD, Ex) from 1 mL to 100 mL
- Density bottles of glass, from 1 cm3 to 100 cm3
如要继续阅读,请登录或创建帐户。
暂无帐户?