Mechanochemical Effect of Severe Plastic Deformations: Metal Alloys, Hydrides and Molecular Solids
Jacques Huot1, Viktor Balema2
1Hydrogen Research Institute, Université du Québec à Trois-Rivières, Trois-Rivières, 3351, des Forges Blvd., PO Box 500, QC, G9A 5H7, Canada, 2MilliporeSigma, 6000 N. Teutonia Ave, Milwaukee, WI, 53209, USA
Material Matters, Volume 5 Article 4
Introduction
Hydrogen, as an alternative to a traditional energy vector such as oil, coal and natural gas, has been the focus of research and development efforts in all technologically advanced countries of the world. It is strongly believed that a hydrogen-based economy can resolve energyrelated problems and slow down global climate change. Hydrogen can be produced from a variety of renewable sources, is non-toxic and as an energy carrier, extremely environmentally benign. However, despite apparent benefits, an immediate incorporation of hydrogen into the world economy faces serious challenges. Although it is routinely used by chemical and refining industries, the cost of hydrogen storage and delivery is too high for the majority of energy applications. Yet, storing hydrogen in solids, metal alloys and hydrides offers a unique opportunity for its convenient and safe use in a variety of portable and stationary applications. This article gives a brief overview of an experimental approach that is used for the preparation and processing of metallic hydrogen storage materials. The approach employs the chemical effect of plastic deformations for nano-scale design and modification of hydrogen absorbing metals and alloys.1 The paper specifically focuses on the methods which introduce severe plastic deformation (SPD) into metal alloys and metal hydrides, and compares SPD to another mechanical processing technique–ball milling. Finally, it also highlights a possible role of plastic deformations in mechanically induced transformations of hydrogen-rich molecular solids, which recently attracted a great deal of interest.2
Severe Plastic Deformations in the Preparation of Metal Hydrides
Severe plastic deformations can be introduced into metallic and intermetallic systems using several relatively simple but very efficient techniques such as: equal channel angular pressing (ECAP), highpressure torsion (HPT) or cold rolling (CR). Similar to high-energy ball milling,2 these techniques were initially developed for the forming and processing of metals but proved to be efficient tools for the preparation and modification of hydrogen storage materials.
Equal Channel Angular Pressing (ECAP) introduces severe plastic deformations into the material by forcing a sample (billet) through a die consisting of two channels of equal cross-section, which intersect at an angle between 90° and 120°.3 (Figure 1)
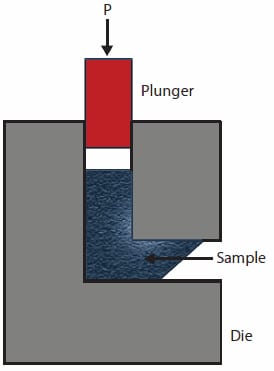
Figure 1.Schematic illustration of Equal Channel Angular Pressing (ECAP)
Since the billet assumes the form and cross-section of the die, it can be repeatedly processed to increase the microstrain and reduce the size of crystallites in the material. In addition, by simply rotating the billet between successive pressings, different slip systems could be activated in the sample. ECAP efficiently processes metals as it enables the production of porosity-free materials with average crystallite sizes between 2 μm and 100 nm in substantial quantities with lower concentration of impurities and at a lower cost than conventional ball milling.4 ECAP has been directly compared to ball milling by Skripnyuk et al., who studied the kinetics and thermodynamics of hydrogen sorption in commercial ZK60 alloy (94.34 wt.% Mg, 4.95 wt.% Zn, 0.71 wt.% Zr) processed by ECAP and/or ball milling.5 Although ECAP proved to be quite efficient in enhancing hydrogen absorption and desorption ability of the alloy, the highest effect was achieved when it was combined with high-energy milling. In another similar study, the investigation of a commercial magnesium alloy AZ31 (96 wt.% Mg, 3 wt.% Al, 1 wt.% Zn) processed by ECAP between 423 K and 573 K,6 also revealed that the optimal hydrogen absorption and desorption parameters of AZ31 were obtained when three different mechanical processing techniques [ECAP, cold rolling (CR), and high-energy ball milling] were combined. Thus, it seems safe to assume that the full advantage of ECAP can be taken if it is combined with other processing techniques, rather than when it is used alone.
In the case of High Pressure Torsion (HPT) processing, a powder or thin film material is subjected to a high pressure and a concurrent torsion straining (Figure 2).

Figure 2.Schematic illustration of High Pressure Torsion (HPT).
s HPT is generally restricted to small (sub-gram scale) samples, it is mainly used to evaluate fundamental effects of SPD in solid materials. One such study was performed by Kusadome, et al. on MgNi2 alloy,7 which does not usually absorb hydrogen. However, after the HPT processing introduced a substantial strain in the material, it became a weak hydrogen absorber (0.1 wt.%) with hydrogen accumulating in grain boundaries of the alloy.7 In another experiment, Lima, et al. observed a substantial improvement in the hydrogen sorption kinetics of a Mg-Fe powder mixture processed by HPT.8 They noted that the hydrogenation and dehydrogenation of the processed samples did not affect the preferential (002) orientation of the Mg phase, i.e., the material retained the microstructure imposed by HPT.
Similarities between HPT and ball milling were evidenced in the recent work by Leiva, et al. who detected the formation of a metastable γ-MgH2 phase and a substantial reduction of crystallite sizes in magnesium hydride, while using HPT to consolidate the metal hydride powder.9 Previously, the formation of γ-MgH2 upon mechanical processing was chiefly associated with high-energy ball milling.10
In Cold Rolling (CR) a sheet of metal is introduced between rollers where it is compressed and squeezed through the roller (Figure 3).

Figure 3.Schematic illustration of Cold Rolling (CR)
The amount of strain introduced by CR determines the hardness and other properties of the finished product.11 Usually, rolling is classified according to the processing temperature as compared with the metal re-crystallization temperature:
• Hot rolling (HR) is the process carried out at a temperature exceeding the re-crystallization temperature of the rolled material
• Cold rolling (CR) is usually performed at a temperature below the re-crystallization temperature
The effect of cold rolling on hydrogen sorption properties of hydrogen storage alloys has been studied in detail.12-14 Zhang et al., investigated the effect of deformations on hydrogen sorption behavior of Ti-based alloys.12, 13 In their experiments, deformations in the material were generated by cold rolling or compression. It turned out that the first hydrogenation (activation) of the cold-rolled alloys was much faster than that of the unprocessed (as-quenched) samples. Unfortunately, this positive effect of CR disappeared after a few hydrogenation/ dehydrogenation cycles as the material returned to its initial state. Couillaud, et al. investigated the effect of a multiple CR on the hydrogen absorption properties of TiV1.6Mn0.4 and compared it to a high-energy ball milling.14 The study revealed that cold rolling and ball milling had a similar effect–both techniques caused the reduction of crystallite sizes and the lattice parameters of the alloy without changing its crystal structure. S. Kikuchi′s group investigated the effect of CR on the hydrogen storage ability of various Mg-based multi-component alloys.15 For the Mg-Ni system, they found that a Mg-Ni laminated composite, subjected to an additional heat treatment, transforms into the intermetallic alloy Mg2Ni, which upon exposure to hydrogen can be converted into the metal hydride–Mg2NiH4. The composition 2Mg+Ni was also studied by Pedneault, et al., who investigated the effect of cold rolling on the electrochemical properties of the processed alloys.16 They found that a combination of CR with an additional heat treatment is a promising approach to the preparation of nanostructured metal hydrides. The nanocrystalline Mg2Ni prepared by cold rolling showed electrochemical performance similar to that of nanocrystalline Mg2Ni powder made by high-energy ball milling from magnesium and nickel. In another example, the laminated Mg-Pd composite materials demonstrate faster activation and better air resistance than the ballmilled samples of the same stoichiometry.17
Cold Rolling of Magnesium and Magnesium Hydride
Similar to HPT and high-energy ball milling, cold rolling of MgH2 (683043) facilitates the formation of the metastable γ-MgH2 phase in magnesium hydride, thus indicating that CR should be at least as energetic as other processing techniques discussed above.9
In recent experiments, J. Huot′s group compared the effects of CR and high-energy ball milling on the hydrogen absorption properties of magnesium hydride. Figure 4 shows the hydrogen absorption kinetics of an as-received magnesium hydride and the samples obtained by ballmilling (for 30 min) or cold rolling (for 5 times).

Figure 4.Hydrogen absorption kinetic at 623 K and under 2 MPa hydrogen pressure of MgH2 in as-received, cold rolled five times (CR5X), and mechanically milled (BM30mins) states.
The untreated magnesium hydride has very slow absorption/desorption kinetics and ball milling for 30 minutes considerably enhances it. Remarkably, the cold rolled sample demonstrates similar kinetics to that of the ball milled material, despite the fact that the rolling was performed in air while the ball-milling was carried out under argon to prevent the material′s oxidation during processing. Thus, cold rolling offers a simple and economical way to modify magnesium, compared to the more expensive and time consuming high-energy ball milling.
It can be expected that the severe strain associated with severe plastic deformations in hydride forming metals, such as magnesium and its alloys, could generate a variety of defects that serve as a nucleation point for the hydride phase. To test this hypothesis, cold rolled magnesium and a commercial magnesium alloy AZ91 (~92% of Mg and ~8% of Al with minor additions of Zn, Mn and Si) were investigated. Each sample was folded and rolled 50 times then exposed to hydrogen. As a reference, a pure untreated magnesium powder was exposed to hydrogen under the same conditions. Figure 5 shows the hydrogen absorption (activation) curves collected at 623 K under the hydrogen pressure of 20 bar.

Figure 5. First hydrogenation (activation) curves of magnesium powder, cold rolled magnesium (Mg ingot) and cold rolled commercial alloy (AZ91 ingot). Activation was performed at 623 K under a hydrogen pressure of 20 bar.
As expected, cold-rolled activated samples demonstrate considerably higher ability to absorb hydrogen in the activation cycle than the untreated magnesium powder. In addition, the rolled samples start to absorb immediately after the exposure to hydrogen, while the absorption by the untreated powder has a long incubation time.
Mechnically Induced Transformations of Molecular Solids
The experimental results presented above clearly demonstrate that severe plastic deformations introduced into metallic materials by Equal Channel Angular Pressing, High Pressure Torsion or Cold Rolling significantly enhance the ability of metals to interact with each other and/or with hydrogen. In other words, severe plastic deformations facilitate mechanically induced chemical transformations in metals and metal hydrides and allow the synthesis of metal alloys and hydride phases ranging from solid solutions to binary and complex metal hydrides (such as Mg2NiH4 or MgH2). It is also safe to assume that the effect of SPD is similar to that of mechanical milling with the major difference being that SPD techniques may offer a less expensive and more scalable way to carry out mechanically activated processes.
To further understand the relationship between SPD and ball milling, it may be helpful to look into the changes that occur in a solid material trapped between colliding balls or balls and container walls during a high-energy ball-mill process. Once trapped between the balls, solid material is subjected to an external pressure causing a sequence of deformations (Figure 6) which starts with reversible elastic deformations followed by irreversible plastic deformations, such as shear and twist deformations. As pressure increases, the latter becomes quite severe and lead to the fracture and/or amorphization of the material.2
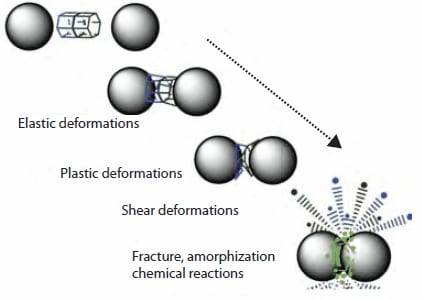
Figure 6.Deformations in the material trapped between two colliding balls during ball milling.
Thus, the character of deformations caused by ball milling are quite similar to those introduced by SPD techniques, which may explain the similarities between these mechanical processing techniques.
For high-energy ball milling, an additional factor to consider is the highpressure generated within the material trapped between the colliding balls and the walls of the milling container. The pressure in such contact areas may reach several GPa,2 making it sufficient to facilitate pressuredriven chemical transformations in metals, ionic hydrides or molecular (organic) solids. However, in a number of cases, very similar chemical reactions are known to occur under conditions that may or may not generate high-pressure spots, but certainly introduce severe plastic deformations into the processed materials. For example, the highenergy ball milling of a mixture of solid phosphonium salts and solid organic aldehydes in the presence on potassium carbonate enables the solvent-free Wittig reaction (Figure 7).18

Figure 7.The mechanically induced solvent-free Wittig reaction.
Initially, the high-pressure generated in the material during ball milling was held responsible for the effect.2 However, further experiments revealed that the use of ball milling is not crucial for this mechanochemical process and the solvent-free Wittig reactions can be run by grinding the reactants with pestle and mortar,19 which shouldn′t generate the ultra-high pressure in the material but is certainly a source of severe plastic deformations similar to those introduced by CR or HPT.
Conclusions
This review of the effects of SPD on the properties of solid materials clearly demonstrates the efficiency of SPD in the preparation and modification of metallic, ionic and molecular solids. For magnesium and magnesium alloys specifically, SPD can enhance the hydrogen storage ability of these materials and improves their hydrogen storage capacities on the first hydrogenation/dehydrogenation (activation) cycle. A similar effect of SPD is also observed for the cold-rolled magnesium hydride. It seems quite feasible that the severe plastic deformations may be also responsible for the chemical effect of mechanical processing of molecular solids, including such complex multi-step transformations as the mechanically-induced, solvent-free Wittig reaction. Amongst the various SPD techniques, cold rolling is arguably the easiest to scale-up to an industrial level. Therefore, it may supersede high-energy milling for the production of nanocrystalline metallic and ionic materials and can likely also be applied to the conversion of molecular (organic) solids. The studies into the application of SPD in materials chemistry of solid materials are at the very early stages of their development and a substantial additional effort is needed to exploit the full potential of this mechanochemical technique.
Acknowledgments
We would like to thank Y. Turcotte, J. Lang and Dr. S. Amira at Université du Québec à Trois-Rivières for help in the study of the effect of SPD.
Materials
References
如要继续阅读,请登录或创建帐户。
暂无帐户?