mAb Downstream Processing
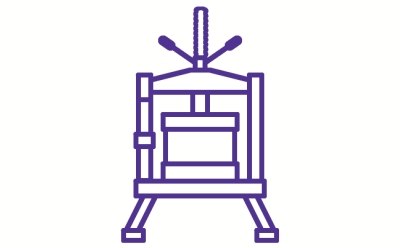
Optimization of the downstream steps in monoclonal antibody (mAb) processing is critical to ensuring product quality, yield, and sterility. Getting the most out of every step depends on a broad range of products, services, and solutions to meet the different needs of each process.
Accelerating clarification of pretreated feed streams
Increasingly efficient upstream processes enable biopharmaceutical manufacturers to achieve higher cell densities and antibody titers. This improved upstream efficiency has led to new purification challenges resulting from high product and contaminant concentrations. Harvest and clarification technologies are evolving to incorporate feed stream pretreatment, including flocculation and different filtration methods such as normal flow, tangential flow, and depth filtration to improve separation efficiency. The objective is to increase process capacities and filtrate quality, while minimizing biomanufacturing costs.
For example, pretreating feeds with a flocculation reagent followed by depth filtration is an effective clarification solution for harvesting high cell density cultures, with easy integration into current platforms. The flocculation reagent acts as a binder to aggregate cells and cellular debris into larger particles within a solution. Primary clarification filters specifically designed for harvesting of high cell density cultures are now available, removing larger particles by using their depth for sieving while maintaining good adsorption capacity.
Featured Categories
Explore our process solution buffer and media preparation solutions, including our Mobius® single-use mixing and Mobius® FlexReady solutions.
Our comprehensive portfolio of high-quality raw materials and functionalized excipients helps you meet the challenges of solid formulation pharmaceutical manufacturing, backed by regulatory support for simplified supplier qualification, accelerated processes, and reduced total cost of ownership.
Downstream and formulation chemicals ensure the yield and safety of your drug product throughout the downstream process. Supporting high-risk applications, our chemicals are multi-compendial and manufactured according to GMP guidelines.
Intensifying mAb polishing with single-pass TFF and anion exchange chromatography
While it is common for mAb downstream purification processes to use a flow-through anion exchange (AEX) resin as a final impurity adsorption step, this conventional polishing step can lead to process bottlenecks due to large columns with long processing times. A growing number of manufacturers are taking advantage of a new solution: pre-concentrating the mAb feed before the AEX column by connecting inline single-pass tangential flow filtration (SPTFF) with AEX chromatography. This approach improves the AEX resin’s capacity for HCP impurities and minimizes the bottleneck at the AEX polishing step.
Increasing purification efficiency using chromatography membrane
Conventional purification technologies generally require trade-offs in process design. For example, resin-based chromatography columns are often oversized due to throughput limitations and are less compatible with flexible manufacturing. Conventional membrane adsorbers offer faster throughput, but their low binding capacity may not provide sufficient process robustness.
To overcome these limitations, a new generation of high-capacity, high-throughput AEX chromatography membrane has been developed, combining high binding capacity and flow rates in a single-use plug-and-play format. This new option for purification offers the potential of more productive, flexible, and robust process design.
Handling high-viscosity feeds associated with increasing concentration
Converting infusion-based treatments to subcutaneous injections can increase patient comfort and satisfaction. The challenges to development of these solutions include:
- Delivering a much higher concentration drug
- Designing an efficient ultrafiltration process, using high-quality formulation buffers
- Overcoming viscosity limitations with some TFF systems
TFF cassettes designed for high-viscosity operation enable drugs to be concentrated without modifying current systems or replacing pumps. Excipient combinations to decrease viscosity of highly concentrated protein solutions can be used to improve process economics during TFF. This can ultimately enable a higher final protein concentration in formulation still administrable with standard syringes.
Optimizing reuse and storage of TFF cassettes
Qualification of TFF cassette reuse, lifetime, and storage is important during optimization and qualification of any manufacturing process. Understanding the requirements and risks of TFF cassette storage and reuse is essential to developing a comprehensive validation plan and mitigating potential risks of product recalls or plant shutdowns.
Optimizing cleaning for extended chromatography resin lifetime
Chromatography resins are a major contributor to monoclonal antibody production costs. To improve process economics and maximize resin lifetime, resins should be effectively cleaned before reuse to remove fouling species.
Optimization of resin cleaning procedures over multiple cycles through traditional lab-scale experiments is time-consuming and requires a significant amount of feed material. However, miniaturized, high-throughput screening tools can be used to optimize resin cleaning procedures. Studies at miniaturized scale accelerate the time to results, while minimizing the volume of feed material and buffers required.
Visit our document search for data sheets, certificates and technical documentation.
Workflow
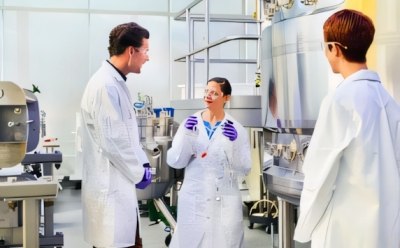
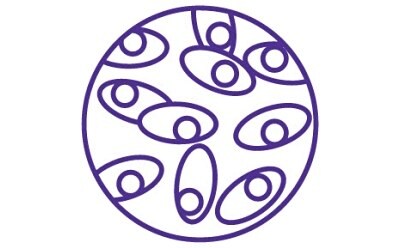
Upstream
The upstream process begins with cell line development and includes all steps up to cell harvest, with the goal of increasing cell densities and product titers to maximize mAb production
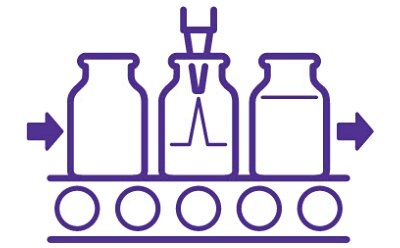
Final Filtration and Filling
Final filling of drug products must meet stringent requirements for sterility, integrity, cleanliness, operational safety, and efficiency
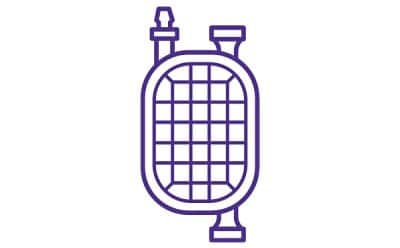
Viral Safety
Based on the principles of “prevent, detect, and remove,” viral safety combines risk analysis with careful selection of raw materials, extensive testing of raw materials and process intermediates, and implementation of virus reduction steps in downstream processing
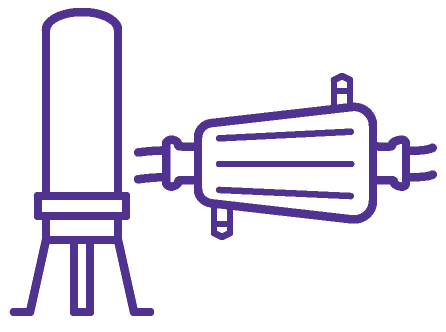
Bioburden Control
All mAb production processes are at risk for microbial contamination, requiring a process design with control strategies to mitigate the risk, as well as bioburden monitoring to assure process control

Aggregate Removal
Protein aggregates are a concern throughout upstream and downstream mAb manufacturing, and control is key to maximizing process efficiency and robustness
Related Articles
- Flocculants, like pDADMAC, remove cell debris during downstream monoclonal antibody production, but their adoption has been difficult due to perceived regulatory concerns.
- Aseptic filters are offered in disposable capsules and cartridge formats. This guide will help you find the right format for your bioburden control.
- Get practical guidance on using single-pass tangential flow filtration in your downstream process and scaling between capsules and cassettes.
- This article outlines critical factors in long-term stability of proteins, and how different stabilizers protect again mechanical and thermal stress.
- Find best practices for using Pellicon® Capsules in ADC processing as well as data from two studies using Pellicon® Capsules and Pellicon® cassettes in the ADC manufacturing process.
- See All (8)
Related Protocols
- This article describes a purification process resulting in low nanoparticulate impurities sucrose, enabling more stable protein formulations.
- See All (1)
Find More Articles and Protocols
Related Product Resources
- Technical Brief: Techniques for Demonstrating Cleaning Effectiveness of Ultrafiltration Membranes
Tangential flow filtration cartridges designed to isolate, purify and concentrate therapeutic biomolecules are typically reused for multiple process cycles.
- Application Note: pDADMAC Flocculant Reagent for Use with Clarisolve® Depth Filters
In recent years, advances in cell line engineering and cell culture media design have allowed for improvements in monoclonal antibody expression, with cell culture systems exhibiting product titers greater than 10 g/L.
- Application Note: Natrix® Q Chromatography Membrane
Comparison of process-related impurity clearance for resin-based chromatography technologies.
- Application Note: Natrix® Q Membrane Adsorber
Comparison of process-related impurity clearance for membrane adsorbers.
- Application Note: Intensified Polishing Using SPTFF with Anion Exchange Chromatography
The bioprocessing industry is interested in Next Generation Processes with higher flexibility, lower costs, and higher product quality.
Related Webinars
Overview of available TFF solutions for achieving high viscosity of monoclonal antibodies and plasma IgG, and strategies for reliable cycle-to-cycle cleaning.
There is growing interest within the biopharmaceutical industry to improve individual unit operation performance by intensification and overall process train efficiency through linked and continuous processing.
How Can We Help
In case of any questions, please submit a customer support request
or talk to our customer service team:
Email custserv@sial.com
or call +1 (800) 244-1173
Additional Support
- Chromatogram Search
Use the Chromatogram Search to identify unknown compounds in your sample.
- Calculators & Apps
Web Toolbox - science research tools and resources for analytical chemistry, life science, chemical synthesis and materials science.
- Customer Support Request
Customer support including help with orders, products, accounts, and website technical issues.
- FAQ
Explore our Frequently Asked Questions for answers to commonly asked questions about our products and services.
To continue reading please sign in or create an account.
Don't Have An Account?