PGM & PGM-free Catalysts for PEM Fuel Cells
Sungjun Kim1,2, Min Her1,2, Yung-Eun Sung1,2
1Center for Nanoparticle Research, Institute for Basic Science (IBS), Seoul 08826, Republic of Korea, 2School of Chemical and Biological Engineering, Seoul National University, Seoul 08826, Republic of Korea
Material Matters™, 2022, 17.1 | Material Matters™ Publications
Introduction
Fuel cells generate energy efficiently through a carbon-neutral electrochemical process, making them one of the most promising energy conversion systems. Among the fuel cells, polymer electrolyte membrane fuel cells (PEMFCs) are the most mature technology and have significantly improved system performance and durability over the past decades. PEMFC applications such as fuel cell electric vehicles have become a reality with these advancements. However, PEMFC commercialization is still limited by high system costs owing to expensive components such as platinum-group metal (PGM) catalysts.1,2 For example, in 2020, the estimated durability-adjusted cost (system cost to achieve 8,000 h of on-road operation) of 80 kW automotive PEMFC system with a production volume of 100,000 units per year was projected to be $76/kWnet, which was higher than the US Department of Energy (DOE) 2025 cost target of $40/kWnet.3 In particular, the PEMFC cost breakdown identified that PGM catalysts accounted for nearly half the total cost of a stack in 80 kW PEMFC systems with a high-volume production scale. Therefore, to realize economically feasible PEMFCs, the primary task is to develop highly active and durable electrocatalysts, especially for the sluggish oxygen reduction reaction (ORR).
Along with a mechanistic understanding of ORR and advances in nanotechnology, there have been great strides in developing innovative ORR catalysts capable of reducing PGM loading while maintaining sufficient activity and stability. Currently, there are two catalyst development strategies. The first strategy is to significantly reduce PGM loading by maximizing PGM catalysts’ activity and durability. The second is to develop a PGM-free catalyst that improves PEMFC performance. In this review, we highlight the recent progress in both PGM and PGM-free ORR catalysts for PEMFC applications. In addition, the remaining challenges in ORR catalyst development that meet the targets of PEMFC applications beyond the preliminary half-cell test are also discussed.
PGM-based ORR Catalysts
The ORR is a complex electrochemical reaction involving various oxygenated intermediates. Pt-based nanoparticles have been commonly used to catalyze the ORR at the cathode. The ORR mechanism is not fully understood; however, fundamental studies using single-crystal surfaces have revealed that the intrinsic ORR activity strongly depends on the adsorption energy of the oxygenated intermediates on the active surface, following the Sabatier principle.4 As shown in Figure 1, Pt is the most suitable single metal catalyst for the ORR. However, pure Pt binds the oxygenated species stronger than optimal; thus, the ORR activity is expected to be at the highest. Thus, the adsorption energy of the oxygenated intermediates on Pt must be weakened to increase the ORR activity. Alloying Pt with other transition metals can tune the electronic structure optimally. For example, incorporating early transition metals (Fe, Co, Ni, etc.) with a smaller atomic radius leads to compressive strain in the lattice, downshifting the Pt d-band center, resulting in a decrease in the oxygen binding energy of Pt. In addition, Pt-alloy catalysts with a core-shell structure, in which active Pt is selectively located on the outer shell over the cheaper transition metal core, enable high Pt utilization. The core transition metal present in the sub-surface below the Pt shell affects the electronic and geometric structure of Pt and can enhance the ORR activity of the Pt-enriched surface. After deliberate acid or heat treatment, a Pt-alloy catalyst can form a Pt-skin shell of an almost pure Pt layer. The resulting catalyst generally exhibits improved intrinsic ORR activity compared to the conventional core-shell type catalyst. Therefore, precise control of the near-surface composition of the Pt shell is essential for Pt-alloy catalysts.

Figure 1.ORR activity plot as a function of the OH adsorption energy (ΔGHO*) for different catalysts with Pt-overlayers. Adapted with permission from reference 4, copyright 2012 Royal Society of Chemistry.
The ORR kinetics on Pt and Pt-alloy surfaces are sensitive to the surface geometry and composition. For instance, the Pt3Ni(111) surface exhibited superior ORR activity compared to Pt3Ni(110) and Pt3Ni(100) facets in 0.1 M HClO4 electrolyte.5 The ORR kinetics sensitivity to surface facet structure has inspired the development of Pt-based polyhedral nanocrystals that can selectively expose specific crystal facets. The most representative example is the Pt-Ni bimetallic octahedra particles reported by Choi et al. Because the octahedral shape could maximize the highly active (111) crystal facets, the particles showed excellent specific activity (3.4 mA cm-2, 51-fold higher than that of Pt/C). Thus, they exhibited 17-fold higher mass activity (3.3 A mgPt-1) at 0.9 V over the Pt/C catalyst despite their low electrochemically active surface area (ECSA) of 31 m2 gPt-1.6 It is difficult to obtain polyhedral nanocrystals with a small particle size because such a metastable structure inevitably changes to a thermodynamically stable spherical shape. It is essential to maintain a highly active surface even in small particles to maximize the active sites at a given electrode for more efficient PGM material utilization. 3D hollow structures have been introduced because they can provide many active sites by exposing both the inner and outer surfaces for ORR while maintaining the highly functional crystal facets. Chen et al. reported a hollow Pt-Ni nano-frame catalyst prepared by selective leaching of transition metals from Pt-Ni polyhedral particles (Pt3Ni NFs in Figure 2).7 The remaining frame not only had a high ECSA (67.2 m2 gPt-1) but also well-exposed Pt3Ni(111) facets with superior ORR activity.
Consequently, the Pt-Ni nano-frame catalyst exhibited ORR mass activity of 5.7 A mg-1 at 0.9 V. In addition to the 3D hollow nanostructure, other structurally modified catalysts have exhibited excellent ORR activity. Li et al. reported an ultrafine, jagged 1D Pt nanowire by dealloying Pt-Ni nanowire (J-Pt NWs in Figure 2).8 The small radius nanowire (~ 2.2 nm) and rough surface with jagged morphology showed high ECSA (118 m2 gPt-1) and superior ORR mass activity of 13.6 A mg-1 at 0.9 V.
Most of these delicately designed Pt-alloy catalysts show excellent initial ORR activity; however, the continuous leaching of the transition metal components during operation makes it difficult to maintain the desired surface composition and structure with superior ORR activity. Although the thermodynamically stable Pt-skin surface can mitigate the metal dissolution, more fundamental approaches to modifying the Pt-alloy system are required to improve the durability of ORR catalysts. Based on experimental and theoretical observations using well-controlled Au-Pt core-shell nanoparticles, our group found that inhibiting the formation of Pt oxide by maintaining a stable structure with low oxophilicity is critical to achieving high stability and ORR activity.9 Thus, one promising approach is to incorporate a more stable third metal component into a bimetallic Pt-alloy system. Huang et al. demonstrated a significant improvement in the ORR activity and durability of Mo-doped Pt-Ni octahedral nanocrystals compared to their bimetallic counterparts (Mo-Pt3Ni in Figure 2).10 Mo atoms preferentially located at the edges of the octahedral particle made the oxidation of Pt and Ni challenging during ORR, thereby inhibiting metal dissolution. An ordered intermetallic Pt-alloy system is another emerging strategy for alleviating the metal dissolution problem. Several seminal studies confirmed that the intermetallic phase is more stable than the disordered phase, and the intermetallic phase can suppress transition metal dissolution.1 However, high-temperature annealing is usually required to obtain the ordered phase, which often causes the coalescence of nanoparticles during the process. To alleviate this problem, our group proposed the concept of carbon-shell encapsulating the nanoparticles.11 By simply coating the disordered Pt-Fe nanoparticle with polydopamine during the annealing process, we obtained highly active, stable, ordered intermetallic Pt-Fe nanoparticles with a thin-layer N-doped carbon shell without any change in particle size. This ordered Pt-Fe catalyst exhibited higher activity and stability than the disordered Pt-Fe alloy and commercial Pt/C in a liquid half-cell condition. Moreover, the ordered Pt-Fe showed good long-term stability under practical operating conditions, showing only a 3.4 % decrease in performance after 100 h operation. During the same period, the performance of Pt/C decreased by 27%. This particular carbon encapsulating strategy is effective in terms of durability even with conventional Pt monometallic catalysts. For example, our group demonstrated that the PEMFC far exceeded the US DOE 2020 durability target using carbon-encapsulated Pt nanoparticles supported on a carbon nanofiber catalyst as the cathode.12 While this strategy is effective in promoting durability, these intermetallic Pt-alloy catalysts do not show superior ORR activity compared to the catalysts mentioned earlier with unique nanostructures. Many intermetallic Pt-alloy catalysts have been successfully applied to single cells due to their high stability.13 Recently, Chong et al. presented a new class of intermetallic Pt-alloy catalysts with a PGM-free catalytic substrate (LP@PF-2 in Figure 2).14 The synergistic effect between the catalytic nanoparticle and the substrate resulted in unprecedented ORR activity under both preliminary half-cell (12.35 A mgPt–1 at 0.9 V) and practical-scale single-cell conditions (1.77 A mgPt–1 at 0.9 Vcell, IR-free). This is an encouraging achievement; however, most PGM catalysts still showed inferior performance under single cell condition in comparison to half-cell condition, they have not been successfully applied to the practical single cell despite their excellent ORR activity (several orders of magnitude higher than that of Pt/C) and durability confirmed in a half-cell system (Figure 2).13
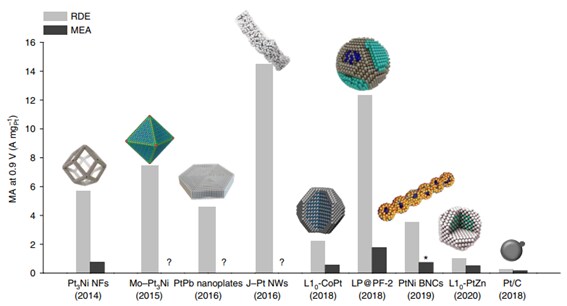
Figure 2.ORR mass activities of state-of-the-art PGM catalysts evaluated in half-cell (gray) and full-cell conditions (black). Reproduced with permission from reference 13, copyright 2021 Nature Publishing Group.
PGM-free ORR Catalysts
Even if the PGM used in the ORR catalyst is reduced through various innovative strategies, PGM is still very expensive, and Pt deposits are limited. Thus, PGM-free ORR catalysts have attracted significant attention. Among the PGM-free catalysts, transition metal and nitrogen co-doped carbon catalysts (M-N-C) are the most promising candidates expected to replace the PGM catalysts in the future.15 In 2009, Lefèvre et al. made a breakthrough in M-N-C ORR catalyst development.16 They fabricated Fe-N-C catalyst by heat-treating carbon black filled with Fe precursor and 1,10-phenanthroline (Cat. No. 131377) in their micropores under an ammonia atmosphere. The Fe-N-C catalyst showed high ORR activity (99 A cm-3 at 0.8 Vcell, IR-free), close to the US DOE performance target for the PGM-free catalyst (130 A cm-3 at 0.8 Vcell, IR-free). After this pioneering work, various M-N-C catalysts were fabricated through high-temperature annealing of carbon materials with various transition metal and nitrogen precursors, from macrocyclic compounds such as metal-porphyrin to simple organic compounds and transition metal salts. Recent advanced analyses such as DFT calculations, X-ray adsorption spectroscopy, and Möβbauer spectroscopy suggest that the M-Nx moiety is the most likely active site.1 Our group confirmed that the intrinsic properties of the active M-Nx sites could be adjusted by modifying their surrounding atomic configuration.17 In addition to tuning the intrinsic activity of the active sites, it is essential to design a catalyst that can expose as many active sites as possible with a large active surface area to achieve high-performance M-N-C catalysts.
Moreover, promising M-N-C catalysts should have an appropriate porous structure that allows quick release of products and easy access to reactant gases and protons. Our group systematically investigated the effect of porous structures on the M-N-C catalysts using a quantitative analytical technique and found that meso- and macropores have different roles in catalysis.18 The mesopores were essential to allow electrolyte accessibility to the catalyst surface, while the macropores facilitated the mass transport of reactants and products on these active surfaces for the ORR.
Conventional M-N-C catalyst fabrication methods have limitations in controlling the density and structure of the active sites. Metal-organic frameworks (MOFs) are an emerging platform for M-N-C catalysts due to a MOF’s ability to precisely control active sites at the atomic level. MOFs can be used as porous carbon frameworks with high surface areas for M-N-C catalysts. During the annealing process, the organic ligands constituting the MOFs were carbonized and converted into porous carbon support. The abundant micropores in MOFs can evenly distribute transition metal and nitrogen precursors.
Additionally, MOFs used for M-N-C catalysts are generally composed of nitrogen-containing organic ligands; thus, they can serve as a nitrogen precursor by themselves, helping to create atomically dispersed M-Nx moieties. Zn-containing zeolitic imidazolate framework (ZIF-8, Cat. No. 691348) is generally used for MOF-based catalysts because Zn (boiling point of 907 °C) easily evaporates during the annealing process (800–1000 °C), thereby forming a highly porous carbon framework.15 Recently, Wan et al. reported a ZIF-8-derived Fe-N-C catalyst with a unique concave structure and high active site density (Figure 3).19 Under the DOE testing protocol, the catalyst exhibited current densities of 47 mA cm-2 at 0.88 ViR-free, cell, exceeding the 2018 DOE activity target for PGM-free catalyst (44 mA cm-2 at 0.88 ViR-free, cell). They achieved high performance of 1.18 W cm-2 under H2-O2 (2.5 bar) conditions using the catalyst.

Figure 3. A)Schematic of the synthesis process

Figure 3. B)TEM image of ZIF-8-based Fe-N-C catalyst with a concave structure (TPI@Z8(SiO2)-650-C).

Figure 3. C)Polarization and power density curves of the catalysts under 2.5 bar H2-O2

Figure 3. D)Tafel plot used to determine mass activity of TPI@Z8(SiO2)-650-C under 1.0 bar H2-O2. Reproduced with permission from reference 19, copyright 2019 Nature Publishing Group.
Despite the excellent performance of M-N-C catalysts, they still suffer from low durability, especially under oxidative and acidic environments at the cathode under practical operating conditions in PEMFCs.15 Although the degradation mechanism of M-N-C catalysts is not fully understood; there is a consensus that the attack by oxidative species such as hydrogen peroxide on M-Nx active sites or carbon matrix is one of the primary degradation mechanisms.20 In Fe-N-C catalysts, oxidative free radicals generated by the Fenton-like reaction of dissolved Fe ions with hydrogen peroxide, a by-product of ORR, exacerbates this problem. Therefore, MOF-based catalysts using other transition metals such as Co and Mn instead of Fe have been developed to mitigate the attack by these radical species.
Summary and Challenges
Recently, several innovative strategies have been proposed to achieve highly active and durable low-PGM or PGM-free ORR catalysts, and various Pt-alloy-based low-PGM catalysts and PGM-free catalysts with MOF-based carbon frameworks showed high activity and stability in preliminary half-cell tests in liquid electrolytes. However, for practical fuel cell operation, the electrode requires a supply of gaseous oxygen to achieve high current operation, making the reactive interface more complex, requiring polymer (ionomers, such as Nafion) instead of liquid electrolytes. Thus, despite their promising activity and stability in half-cell conditions, most ORR catalysts still show inferior performance and durability in more complex and harsher single-cell conditions. This discrepancy in performance between half-cell and full-cell shows that the material must be designed with consideration for practical full-cell applications from the early stage of development of ORR catalysts. Therefore, it is necessary to better understand the physicochemical phenomena occurring at the catalyst-ionomer interfaces in a full-cell electrode beyond a liquid half-cell system.
Author Contributions
The manuscript was written through the contributions of all the authors. All authors approved the final version of the manuscript.
Notes
The authors declare that they have no known competing financial interests.
Acknowledgment
This work was supported by the Institute for Basic Science (IBS-R006-A2).
Materials
References
如要继续阅读,请登录或创建帐户。
暂无帐户?