Rare Earth Crisis—Supply/Demand Situation 2010–2015
K.A. Gschneidner, Jr., Ames Laboratory, U.S. Department of Energy and Department of Materials Science and Engineering
Iowa State University
Introduction
The rare earth elements impact nearly everyone in the world. All of the people living in advanced technological countries and almost all those living in third world countries utilize the rare earths in their everyday living—the car that one drives (gasoline is refined from oil using rare earth catalysts and catalytic converters reduce the polluting emissions from the automotive exhaust), watching the news on TV (the red and green colors in TV screens), the telephones and computers we use to communicate (the permanent magnets in speakers and disc drives), just to name a few examples. For a more complete listing, see Table 2. The only way you can avoid the rare earths is to grab your sleeping bag and go into the deep forests or caves in the desert far from civilization without your cell phone or even lighter flints (which are made of iron and cerium-rich rare earths). In addition to the impact on our personal lives, the military security of the USA (and the rest of the world, likewise) is very dependent on the rare earths (permanent magnets in electric motors, computers, and guidance systems): this is also the case for our energy security (electric motors, batteries, wind turbines, petroleum refining, and fluorescent lighting). Today, 97% of the rare earths used in commerce come from mines in China (primarily the bastnäsite Bayan Obo mine, Inner Mongolia), about 2% from India, and about one-half percent or less each from Brazil, Malaysia, and the USA. This precarious situation does not bode well for the technological future of the USA and the rest of the non-Chinese world (ROW). Although the ROW can get most of the rare earths needed, the prices for Chineseproduced elements have increased by about 100% over the past year, and as much as 900% for a selected one or two rare earths—surprisingly La and Ce.
As seen in Figure 1 the rare earth elements are reasonably abundant and lie between the 25th and 75th percentiles of natural abundance of the elements, with cerium being the most abundant rare earth and lutetium the least. The commonly mined rare earth minerals are given in Table 1. It is not that the rare earths are only found in China; viable deposits are known to be located in almost any corner of the world. China has about 31% of the known reserves, while the USA has one of the best minable deposits in the world—Mountain Pass, California, which is about 75 miles west of Las Vegas on Interstate 15, about 5 miles inside the California/Nevada border. If this is the situation, how did we (the ROW) get into this dilemma? And how will the ROW extract itself? Some of the answers follow in the succeeding paragraphs.
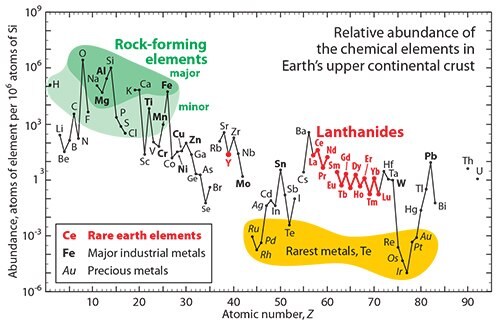
Figure 1.Relative abundance of rare earths (highlighted in red). Figure courtesy of Gordon Haxel, USGS.
History
The production of the rare earths was ~2 ktons per annum before 1960, and it grew at a rate of about 10% per year, up to 124 ktons in 2010. The discovery of the intense red luminescence of Eu when excited by electrons, which was quickly utilized in color TV in the early 1960s, was the start of the growth process of the rare earth industry. Production of rare earth oxides from Molycorp′s Mountain Pass, California bastnäsite deposit started in 1964, and within two years the company supplied 50% of the rare earth oxides consumed in the world, continuing to do so until 1984. In 1985, China began to export mixed rare earth concentrates, and by 1990, its production exceeded that produced in the USA. In the early 1990s, China began to export separated rare earth oxides and metals, and reduced the amount of mixed rare earths supplied to the rest of the world. By the late 1990s, the Chinese continued to move up the supply chain to higher value products such as magnets, phosphors, and polishing compounds. Since the turn of the century, China has supplied finished products including electric motors, computers, batteries, liquid crystal displays (LCDs), mobile phones, and portable music devices. More details concerning these changes can be found in recent articles published in Science,1 Chemical and Engineering News,2 and Bloomberg/Business Week.3
In 1970, China had 75% of the known rare earth reserves and, based on this, started to demonstrate a strong presence in the rare earth markets. However, in the subsequent 30 years, the percentage of Chinese reserves dropped to about 30% because of the discovery of new deposits all over the world, even though the absolute amount of the known Chinese reserves grew by about 290%. Recently, China has changed its approach to the rare earth market, and they have introduced production quotas, export quotas and export taxes, enforced environmental legislation, and granted no new rare earth mining licenses. Furthermore, China has stated that they will no longer export rare earth-finished products, because of rapid growth of internal markets and limited reserves, especially the heavy rare earths (Gd through Lu). As a result, the price for rare earth materials and products containing rare earths has risen to a level at which the ROW mining companies and producers can be competitive and make a profit. The non-Chinese production of rare earth oxides (REO) per year was estimated to be 4 ktons in 2009. There is another important source of rare earth materials: those that are smuggled out of China; most of which are the highly valued heavy lanthanides and yttrium coming from South China′s xenotime and laterite clays deposits. The black market was estimated to be 30-40 ktons in 2007, i.e., about 20% of the officially published numbers. Naturally, the Chinese government is trying to stop this leakage, and they seem to be successful since the latest estimate decreased to about 15-20 ktons in 2010.
The various applications for the mixed and the individual rare earths are presented in the fourth column of Table 2 Also listed are the estimated current demand (column 3) and the percentage of a given rare earth commodity relative to the entire market (column 2 and Figure 2). The market situation for each rare earth—balanced, surplus, tight (shortage)—is also noted in Table 2 (column 3). The largest markets are Ce (30% of the total by weight), mixed rare earths (28%), La (25%), Nd (16%) and Pr (5%). Of the ten remaining other markets, three are 2% or less (Sm, Gd and Dy), and the other seven account for less than a half of a percent each. It is noted that only about 43% of the cerium mined today is utilized, and if it were completely utilized cerium′s share of the market would be nearly 50%. Even though cerium is relatively inexpensive to separate compared to the other rare earths—a simple oxidation/reduction process—it must be first removed from the flow stream in order to begin the processing of the other rare earths by a counter current liquid/liquid extraction process.
There is also a second penalty: it must be stored (about 50 kton per year). The rare earth industry would greatly welcome new, large (tens of ktons) cerium applications. If the cerium market were balanced, it would significantly reduce the costs of the other rare earth elements. The rare earth usage by various applications is shown in Figure 3. Shown in Figure 4 are some high purity (research grade) rare earth metal, oxide, and fluoride samples produced at the Ames Laboratory′s Materials Preparation Center.4
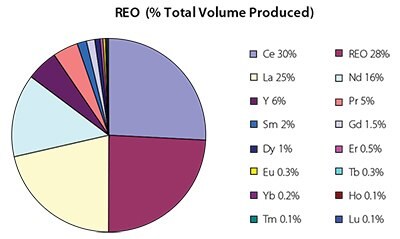
Figure 2.Distribution of rare earths by percentage of total volume produced. REO reflects mixed metal rare earth oxides.
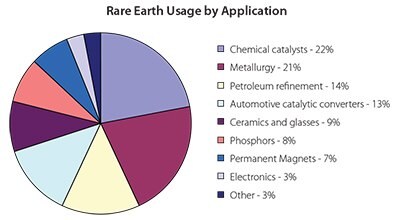
Figure 3. End use distribution of rare earth elements by application in 2009. Data from USGS Mineral Commodity Summaries.
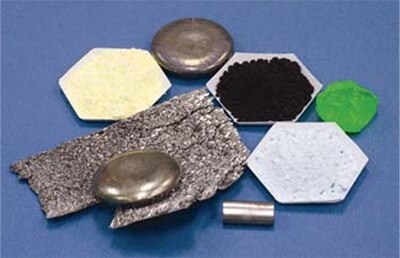
Figure 4.Rare earth metals (arc-melted buttons and a cast rod), oxides (powders), and fluorides (crystals). Source: Ames Laboratory.
Future
Mining
The best forecast suggests that ROW mining companies need to increase their output of 6 ktons in 2010 to 50 ktons in 2015 to meet the growing demand. It is anticipated that the Mountain Pass mine will be in full production in 2012, supplying 20 kton/year and doubling that amount in the second phase of their expansion in 2013. The Mount Weld monazite mine in Australia will start production in 2011 and will be able to supply 21 kton/year in 2013. These two companies should be able to make up most of the projected demand through 2014-2015. These two deposits, however, contain predominantly the light rare earth elements (La, Ce, Pr, Nd and Sm). The demand for Nd and the heavy rare earths Tb and Dy will be tight for the 2011-2015 semi-decade. There are a number of smaller deposits with a large fraction of these three elements, which are expected to come on stream in the 2014-2015 time frame, potentially easing the pressure for the heavy rare earth elements.
The two important non-Chinese mines in operation today are the Orissa placer deposit (Toyota, India) and the bastnäsite Dong Pao mine (coowned by several Asian companies, Vietnam). Both are producers of the light lanthanides and account for about 5 kton REO from the ROW. Five additional light lanthanide rare earth mines are anticipated to become operational in the 2013-2015 period. In addition to these ten sources, there are between 100 to 150 deposits that have been promoted as possible rare earth sources, but most will never become fully functioning mines. If most of the promising new mines and the established ones come on stream, there will be an excess of rare earth oxides in the market in the 2015-2020 time frame, assuming the demand increases by 10% per year.
Mid-supply Chain and Original Equipment Manufacturers
Although it appears that the mined ores, the processed rare earth concentrates, and the separated individual rare earths should meet the 2011-2015 demand for these starting materials, the major problem will be absence of ROW manufacturers in the supply chain to convert the rare earth oxides into useful products, e.g., magnets, batteries, phosphors. This also applies to the ROW original equipment manufacturers (OEM) of the final products [such as computers, electric motors, cell phones, compact fluorescent lamps (CFL), LCDs, and batteries] since they were driven out of business in the 1990s. It does not make much sense to mine and process the rare earth starting materials in the U.S. and send them to Asia for final product production before shipping them back to the United States.
The U.S. and ROW governments need to take vigorous action to reestablish mid-supply chain and OEM industries which can effectively compete on a global scale. The most direct way to invigorate the midsupply chain and OEMs is to establish long-term guaranteed loans to these organizations to convert the mined rare earth oxides to metals for magnets, batteries, and magnetic refrigeration systems, and to other useful compounds for phosphors, optical components, catalysts, etc. These companies need to modernize, using the latest available technologies and automate the production processes—this is the only way we will be able to effectively compete on a global scale.
Training Scientific and Engineering Personpower
The lack of trained and experienced scientists and engineers, especially those younger than 50 years old, to fill in these technological gaps in the supply chain also contributes to the ROW′s dilemma. Many of the older living scientists and engineers who were working for firms in the rare earth supply train have either retired or moved on to new positions and are not likely to come back into the rare earth industry. The lack of an intellectual infrastructure can be addressed by establishing a National Research Center for Rare Earths at an educational institution with affiliations with other universities, colleges and research centers. This was recently discussed in more detail by the author.5
Upon completion of their studies, the students will enter the workforce, i.e., industry, educational institutions, government, non-profit laboratories, etc. There is another five to ten years on the average before they reach their full potential. This is the point, and beyond, where they invent new products, design new and improved processes to make the new and the old mature devices and products more economical (and perhaps simultaneously by environmentally green technologies), become our future educational leaders, and make other scientific and technological contributions to society. These are the persons who will help regain our technological leadership and inventiveness that we once had in the 1980s and early 1990s. Thus, the Center′s mission should be completed in a 10-to-15-year framework from the date it starts—a long time, but a big pay off. This is a chance the U.S. and ROW need to take.
Other Solutions
At the present time, there is little to no recycling of rare earth-containing products, except in Japan, but some research efforts have been started, at least in the U.S. It is likely that more research on this topic will be funded by the ROW national governments. One of the major problems is that although the rare earths are essential components of electronic devices, etc., they only constitute a small fraction of weight/volume of the final product (e.g., a computer). As a result, the percentage is about the same as that of the poorer ore bodies (i.e., ~2%) which are mined today. For cell phones and portable music devices it is much worse, the rare earth magnets weigh less than 0.1% of the device.
Currently, there is a small effort to find substitutes for the rare earth elements, but this is a difficult task due in part to their unique electronic structure and the unique properties of the 4f electron orbitals. The major high technological applications (optics, phosphors, fluorescent lighting, electronic devices, magnets) of the rare earth (lanthanide)-based materials depend upon the specific 4f electron configuration of each element. Therefore, the applications are quite unique, making it difficult to find other elements to substitute for the rare earth atom, even one lanthanide for another. The odds of finding a substitute for a particular rare earth range from slim to none depending on the application. Scientists and engineers have been looking for substitutes from day one when the new application became viable. For example, the red color in TVs is due to Eu—it has been around for over 50 years and no substitute has been found; likewise, over 30 years have passed for the Sm permanent magnets (692859, 692840, 692832) and the 3-way Ce automotive catalytic converter, and about 27 years for the Nd-Fe-B (693790, 693782, 693820) permanent magnets, and still no viable substitutes demonstrating identical performances have been found. It is not that we should not try, but we must realize that success is not very likely.
However, partial substitution of one lanthanide by another may extend the utilization of the parent lanthanide. For example, partial substitution of Pr for Nd in the Nd-Fe-B permanent magnets is possible, but since there are about 4 Nd atoms per 1 Pr atom in the original ore source, this merely reduces the amount of Nd used in these permanent magnets, but it has the additional advantage in that Pr is not a by-product which must be stored. Another situation is the replacement or partial substitution of La in the nickel metal hydride (685933) battery by mischmetal (a metallic mixture of the naturally occurring rare earth ore—50% Ce, 25% La, 15% Nd, 4% Pr). In both cases there is some reduction of the performance of the magnet or the battery, but the properties are still sufficient for some applications.
There is one possible viable substitution of the rare earth permanent magnets in direct drive wind turbines and that is to use the high temperature ceramic YBa2Cu3O7 (328626) superconductor operating at ~50 K to generate the magnetic field.6 This, however, trades one rare earth (Y) for another (Nd), and this would put pressure on the Y market, which is currently in balance, to relieve the pressure in the Nd market. Is this a good trade-off?
One can always go back to the product that the rare earth replaced and use it instead. But would the user accept the inferior performance? For example, laptop computers would be about 50% bigger in size and weigh twice as much. Similarly, the automotive industry would have to return to heavier and bulkier electric motors, and as a result, reduce the mileage one gets from a gallon (liter) of gasoline—this is not likely, since automotive companies are striving very hard to meet government CAFE (corporate average fuel economy) standards (35.5 miles per gallon in 2016) to increase the number of miles one gets from a gallon of fuel.
There is a great deal of uncertainty about the future rare earth markets because of the size of China′s market share of rare earth supplies and refining. Additionally, China claims that in a few years (by 2015) they will no longer supply any rare earth materials to the ROW because they expect their internal rare earth consumption will utilize all of the domestically mined rare earths. The question is, will they begin to import some rare earths, primarily the heavy lanthanides plus yttrium after 2015? Or will they increase their internal production? The former is the most likely scenario because Chinese mining companies are actively trying to buy major ownership in global rare earth ore sources, especially those that have a predominance of yttrium and heavy lanthanides. This is because their ion absorption (laterite) clay deposits are expected to be depleted by 2025 or earlier. This leaves them with only one known xenotime deposit in Guangdong as their primary source of heavy rare earths.
China appears to be continuing to control their share of the rare earth market at the mining, beneficiation, and initial separation stages (i.e., they are no longer exporting these commodities). Using these materials internally directly affects the supply of rare earth products further up the supply chain, where the ROW is the weakest due to the demise of the technical, scientific, and entrepreneurial rare earth infrastructure, which deteriorated in the late 1990s and early 2000s.5
It is extremely unlikely that Chinese producers will lower their prices of the entire rare earth market as they did initially to establish a strong market presence (roughly 1992-2005). They may, however, lower prices on selected rare earths for some economic advantages. Regardless, the ROW can meet the growing demand for rare earth materials by reestablishing mining, processing, and refinement capabilities; developing the mid-supply chain and production of finished products; and training the next generation of scientists to contribute to the rare earth industry.
Acknowledgments
The author thanks his colleagues V.K. Pecharsky, A.H. King, I.E. Anderson and S.R. Karsjen, and Nathaniel Henderson for their constructive comments. Work at Ames Laboratory is supported by the Office of Basic Energy Sciences, Materials Sciences Division of the Office of Science of the U.S. Department of Energy under Contract No. DE-AC02-07CH11358 with Iowa State University.
Materials
References
To continue reading please sign in or create an account.
Don't Have An Account?