Titania Nanotubes: Synthesis & Apps
Eugen Panaitescu1, Latika Menon2
Department of Physics Northeastern University, Boston, MA 02115 USA
Would you like to be notified by email when we publish new technical papers related to battery development? If so, click the subscribe button to complete a short form. Your information will be kept private, and you can unsubscribe at any time.
Introduction
Titania (titanium dioxide, TiO2) (Prod. Nos. 799289, 204757, 232033, 248576, and 677469) is a versatile earth-abundant ceramic with many desirable properties such as high melting point (>1,800 °C) and stability under adverse chemical conditions. Electronically, it behaves as a wide band gap (3.2 eV) semiconductor and exhibits memristor properties. Optically, TiO2 has high opacity with a very high refractive index (>2.4), and it exhibits strong absorbance in the UV range. It is an excellent catalyst because of its strong oxidative potential, especially when exposed to UV light. As a result of these properties, titania finds a wide range of applications in white/opaque pigments, coatings and sunscreens (protection from UV radiation), antifogging coatings, ceramic filtration membranes, antimicrobial coatings, photocatalysis, and photovoltaics (e.g., dye-sensitized solar cells—DSCs). In the nanostructure form, titania exhibits additional features such as high porosity and surface area. For example, titania nanotubes (TiNT) (Prod. No. 799289) possess high porosity (50–200 m2/g) and high active surface area (2–3 orders of magnitude higher than a flat surface). These features greatly enhance the efficiency of the aforementioned applications and make them suitable for new applications like highly oleophobic filtration membranes for water-oil separation and anodes for fast-charging lithiumion batteries. We have identified a wide array of potential applications for TiNT. A summary of some of these promising applications, either in as-is form or integrated with other (nano) materials and incorporated into complex structures or devices, is presented in Table 1.
Synthesis of Titania Nanotubes by Electrochemical Anodization
Historically, many different methods such as electrochemical deposition in nanoporous alumina templates, sol-gel methods, seeded growth, electrospinning, and hydrothermal methods have been employed for the synthesis of TiNT. However, in general, these are complex, multistep methods that are hard to scale up beyond lab scale and result in a low yield of nanotubes. Synthesis of TiNT by means of electrochemical anodization of titanium in fluoride-ion containing electrolytes was developed relatively recently. This is a simple, cost effective, easily scalable method resulting in highly ordered arrays of vertically aligned nanotubes and has become the standard synthesis method for TiNTs. The mechanism for nanotube formation is very similar to that of nanopores in anodic aluminum oxide (AAO), a well-known and extensively reported material. The synthesis of TiNT is initiated by the application of a DC bias voltage in the presence of the electrolyte containing both oxidizing and reducing agents to form an oxide layer on the surface of the metal anode (Al or Ti). This is followed by the field-enhanced dissolution of the oxide, which results in corrosion pits. When equilibrium between oxidation and dissolution is reached, the corrosion pits grow continuously into vertically aligned nanopores or nanotubes. Because nanotubes produced by anodization are amorphous, the samples must be annealed in air, oxygen, or a nitrogen atmosphere at 300–500 °C, with a slow heating and cooling rate (1–5 °C/min) to produce crystalline material. The resulting structure is anatase (polycrystalline) with a crystal size of approximately 25 nm.
A significant advantage of anodization over other fabrication methods is that it offers precise control over the shape, structure, and morphology of the produced nanotubes simply by controlling different synthesis parameters. For instance, anodization voltage can be used to control nanotube diameter, while the time of anodization can be modified to control the average length of the tubes. The viscosity, pH, and concentration of fluoride ions within the solution influence the oxide dissolution and rate of chemical reaction. These parameters have a direct effect on the tube formation rate, maximum achievable tube length, and smoothness of the tube walls. The water content controls the strength of the attachment between the nanotube arrays and the original Ti substrate. Some typical TiNT morphologies that may be obtained are listed below.
- Low Aspect Ratio TiNT Arrays (Figure 1A) Up to 6:1 aspect ratio (30–80 nm diameter, 100–500 nm length) TiNT arrays can be obtained by anodization for less than an hour at anodization voltages between 10 and 20 V DC in 0.1–0.4 M HF solutions. The tubes are quasi-ordered, form rapidly, and are uniformly distributed over the entire sample surface.
- High Aspect Ratio TiNT Arrays (Figure 1B) Up to 100:1 aspect ratio (50–150 nm diameter, 2–8 μm length) nanotube arrays can be obtained by anodization for 3–8 h at anodization voltages between 10 and 30 V DC in aqueous solutions containing fluoride salts (KF, NaF, NH4F), buffered in order to lower the acidity (pH up to 4). Well-defined and well-ordered nanotubes arrays are produced. The key disadvantage of this method is the requirement of long anodization times.
- Ultra-high Aspect Ratio, Highly Ordered TiNT Arrays (Figures 1C, D) Over 1,000:1 aspect ratio (90–200 nm diameter, length up to mm range) nanotube arrays can be obtained by anodization at 30–60 V DC in non-aqueous solutions containing fluoride salts, using solvents such as formamide (Prod. No. F7503), DMSO (Prod. Nos. 276855 and 472301), ethylene glycol (Prod. Nos. 324558 and 102466) or glycerol (Prod. No G7757). Smooth, well-defined, and quasi-hexagonally ordered nanotubes are obtained. When the water content in the electrolyte is reduced to a minimum, the TiNT can detach from the Ti substrate, and free standing arrays of TiNT can be obtained (Figure 1D). Length of the nanotubes can be tailored by controlling the time of anodization and can range from approximately 15 μm for 2 h anodization to 30 μm after 6–8 h, and 50+ μm for over 24 h of anodization. In these cases, the maximum possible length of the nanotubes is typically limited by the thickness of the original Ti foil.
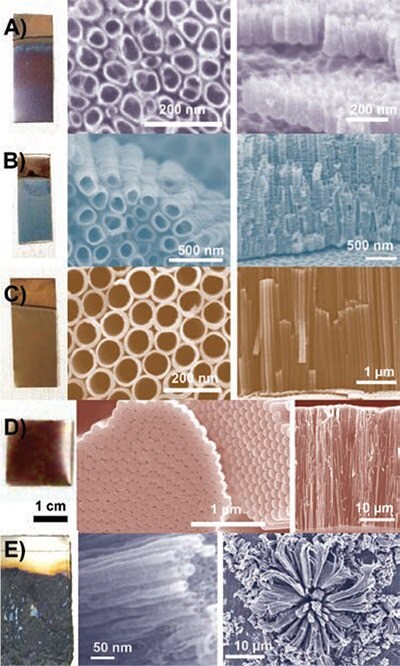
Figure 1.Digital pictures of the samples and frontal and side-view SEM images of titania nanotube samples fabricated in a variety of shapes and morphologies. A) Short nanotubes (<500 nm). B) Medium-length nanotubes (2–5 μm). C) Long and ultra-long nanotubes (30–700 μm) attached to the original support. D) Free-standing (bottom view shown here indicating that the tubes are closed, top view is similar with C). E) Ultra-long nanotube bundles (up to 60 μm) formed in corrosion pits scattered all over the sample.
Anodic TiNT arrays can be integrated with materials such as metals, metal-oxides, or polymers by various physical, chemical, electrochemical, or electrophoretic methods for optimized applications and devices. For example, gold (Figures 2A, B) or iron oxide (Figures 2C, D) nanoparticles (Prod. No. 544884) can be easily attached to the nanotubes using simple deposition-precipitation methods.
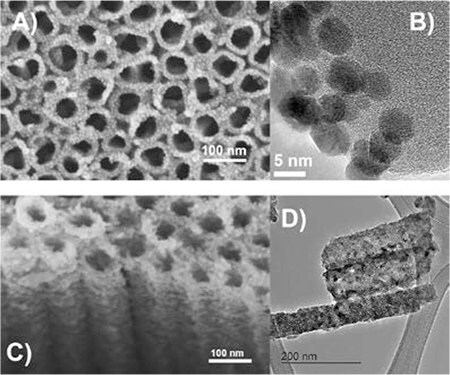
Figure 2.A) SEM and B) HRTEM images of TiNT arrays deposited with gold nanoparticles. C) SEM and D) TEM images of iron-oxide (hematite) decorated TiNT arrays.
Anodization in Chloride-ion Containing Solutions
Our recent work demonstrated the fluoride-ion electrochemistry-based nanotube formation mechanism can be replicated using chloride-ion containing solutions. Besides eliminating the toxic fluorides from the synthesis process, the new method also results in significantly accelerated reaction rates, reducing tube formation time from tens of minutes and hours to tens of seconds. In this accelerated process, the corrosion pits evolve differently, and the titanium substrate does not have sufficient time to accommodate the increase in volume associated with the rapidly forming nanotubes. As a result, tightly bound nanotube bundles are expelled into the solution (Figure 1E), appearing as a white powder after washing and recovery from the solution. Bundles of nanotubes with an aspect ratio of over 1,000:1 (25–50 nm diameter, lengths up to 60 μm) can be obtained by anodization in aqueous (at DC voltages between 10 and 16 V) and non-aqueous solutions (at DC voltages between 30 and 60 V) containing chloride salts such as KCl, NaCl, or NH4Cl. The bundles are tightly packed with cross-section areas varying from submicrons (effectively containing a few tens of nanotubes) to a few square microns (with tens of thousands of nanotubes). Though ordering of the nanotubes is limited to a few tens of microns at most, and the coverage of the titanium foil with corrosion pits is not uniform, this method provides a much faster route for nanotube production. Gram quantities of ultra-high aspect ratio TiNT powders can be obtained after 60–100 min of anodization.
Applications: Photocatalysis
The photocatalytic properties of TiO2 are based on its ability to generate electron-hole pairs under illumination, which then promote redox reactions such as electrolysis. The discovery of TiO2-photocatalyzed water electrolysis in 1972 triggered enormous interest in the material for hydrogen production and for other photocatalytic applications. TiO2 has been shown to be the most useful photocatalyst for numerous environmental applications due to its biological and chemical inertness, and resistance to photocorrosion and chemical corrosion. The three main photocatalysis applications—water splitting, organic compound decomposition, and inactivation of bacteria—are discussed in the following sections.
Hydrogen Generation by Water Photoelectrolysis
Photoelectrochemical generation of hydrogen by using TiNT has been studied extensively since the discovery of the new nanostructures 15 years ago. Park et al. showed the nanotubular structure indeed enhances the photocatalytic activity of TiO2 in water splitting by maximizing solar energy harvesting. Water splitting efficiency is significantly improved by optimizing structural and morphological parameters such as wall thickness, length, and crystalline structure (anatase) of the nanotubes. Band gap reduction by carbon doping or the addition of other metal oxides with narrower band gaps results in an increased hydrogen evolution rate. Our group demonstrated the adsorption of low quantities of sodium or potassium on the nanotube walls using sodium or potassium fluoride in the anodization solution used during the synthesis can result in increasing the overall efficiency of the photoelectrochemical process.
Oxidation and Decomposition of Organic Compounds
The strong oxidation properties of titania under illumination can be employed in the decomposition of organic pollutants. The mechanism for degradation of organics is similar to that of water splitting. In aqueous solution electron-hole pairs are created in TiO2 under exposure to a light source. These electron-hole pairs migrate to the surface and react with absorbed organic molecules, causing them to decompose. The photocatalytic activity exhibits more dependence on the specific surface area than the crystal phase of TiO2. Efficient photoactivated demineralization of organic compounds by using membranes consisting of free-standing arrays of TiNT has also been demonstrated, opening the possibility for multifunctional, self-cleaning filtration membranes.
Light-enhanced Antimicrobial Activity
TiO2 has been used as a photocatalyst in antimicrobial applications as well. Under the irradiation of UV light, the generation of electrons at the conduction band and holes at the valence band in TiO2 produce hydroxyl radicals (OH), superoxide radicals (O2-), singlet oxygen (1O2), peroxide radicals (OOH), and hydrogen peroxide (H2O2). These reactive oxidation species result in physical damage to the cell membranes, leading to cell death. Recent work with TiNT powders performed by our group, using Escherichia coli (E. coli) and Staphylococcus aureus (S. aureus) as the target microorganisms, revealed excellent antibacterial properties of the powders compared to commercial anatase nanoparticles (Degussa P25) (Prod. No. 718467) after 24 h of UV exposure. Specifically, 97.53% of E. coli and 99.94% of S. aureus were destroyed after 24 h, while the commercial nanoparticle lost its antimicrobial properties after 1–6 h. Also, it was demonstrated the architecture, surface, and physicochemical properties of TiNT along with specific experimental conditions of the biological investigation, play a significant role in the disinfection activity.
Applications: Photovoltaics
The main application of nanostructured titania is in DSCs, one of the most promising among numerous third-generation photovoltaic technologies. DSCs provide acceptable solar energy conversion efficiency (>10%) by employing a much simpler structure, scalable fabrication route, and lower production costs compared to the silicon-based solar cells. Typical DSCs consist of a wide band gap n-type semiconductor working as an electron conductor coated with dye, a liquid electrolyte for hole conduction, and two transparent conductive electrodes such as conductive indium-tin oxide-coated (Prod. No. 703192) glass. The photovoltaic process in DSCs begins at the interface between the semiconductor and dye. The electrons in the dye are excited by light and are rapidly transferred to the conduction band of the semiconductor. TiO2 is by far the most widely used semiconductor due to its excellent physical and chemical properties. The electrons pass through the external load and transport back to the counter electrode, which is in contact with the liquid electrolyte. The dye is regenerated by the ionic transport of a redox couple in the electrolyte.
In the past 10 years, several TiNT-based DSCs have demonstrated power conversion efficiencies approaching 10%. The uni-dimensional morphology of the nanotubes provides a natural pathway for the conduction of electrons that is not limited by the intergranular scattering prevalent in nanoparticulate titania films. Scattering from crystal grain boundaries cannot be avoided due to the fact the nanotubes are polycrystalline, thus resulting in similar electron mobilities for both tubes and particulate films. Recombination times in the nanotubes are much improved (by at least one order of magnitude), resulting in superior charge collection efficiency. The electron diffusion length is large enough and the hollow nature of the nanotubes allows for light trapping and overall deeper light penetration. As a result, thicker nanotube layers (up to 100 μm) could be effectively used24 for enhanced cell efficiency, while nanoparticulate titania layers thicker than 10–20 μm can be detrimental to performance.
TiNTs are being studied for other emerging solar cell concepts. For example, in partnership with industry our group is developing fully solid-state, ultra-low cost metal oxide solar cell prototypes for niche applications. Perovskite cells are also gaining attention exponentially, and a TiNT-based flexible perovskite cell with efficiency of up to 8.3% has been recently demonstrated.
Conclusion
There has been intensive research on anodic titania nanotubes since their first discovery 14 years ago. The number of annual publications on anodic TiNT has been steadily increasing, exceeding 600 in 2012. Numerous applications are envisioned capitalizing on the synergistic combination of desirable material properties of titania and the enhanced active surface area offered by the unique, controlled architecture of nanotubes. This article discussed two of the most promising applications in the energy sector, namely photocatalysis and photovoltaics. Applications in other high-impact fields such as clean technology, biotechnology, and batteries also may become viable once titania nanotubes are available commercially to R&D groups for quick testing and prototyping.
Materials
References
如要继续阅读,请登录或创建帐户。
暂无帐户?